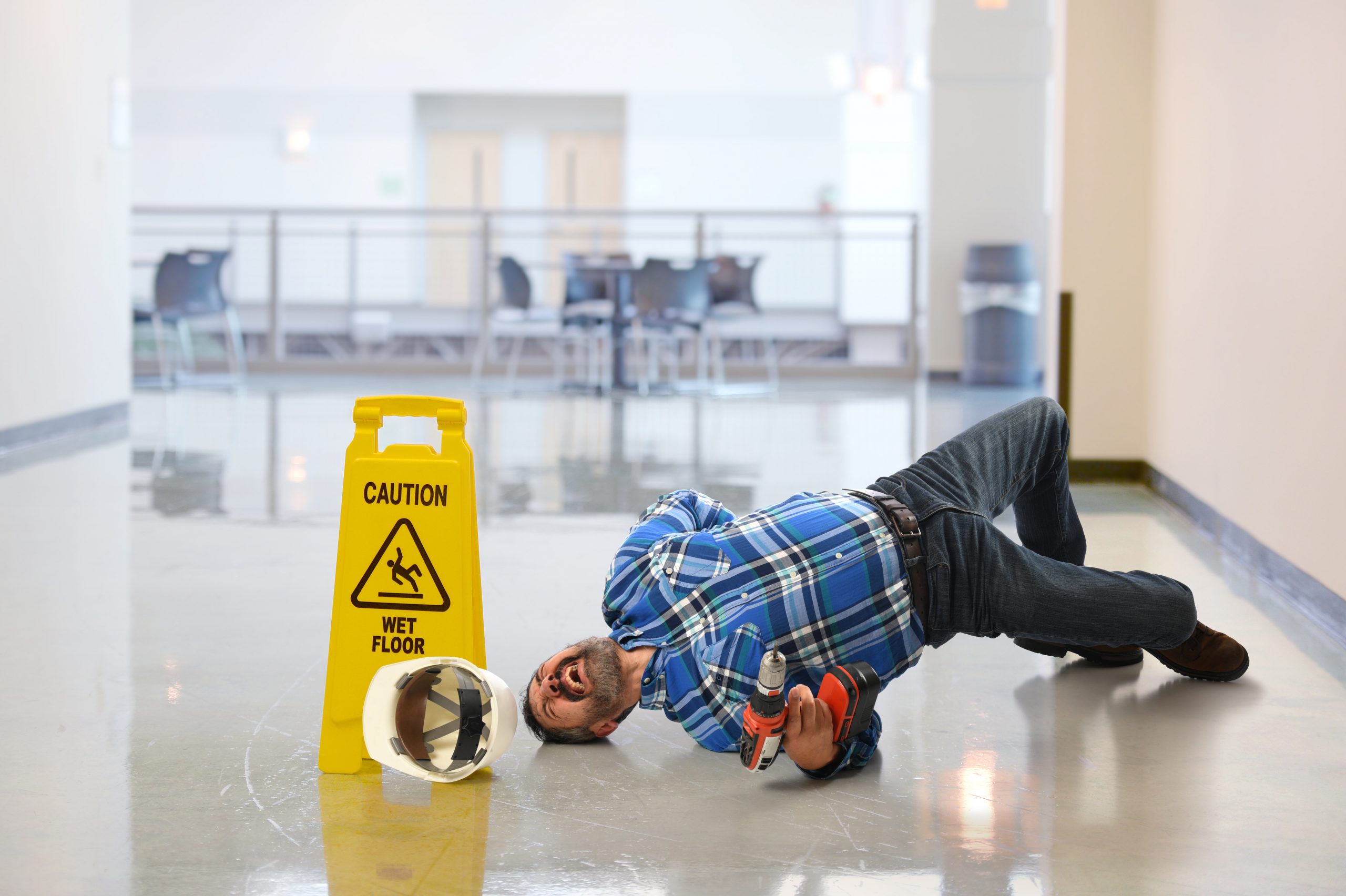
If you don’t get your pallet racking inspection frequency right, you could fall victim to some of these lesser-known dangers.
HSE’s stance on racking inspection frequency is that every warehouse should have at least one inspection from an expert, such as a SEMA approved racking inspector, once a year and that regular racking inspections should be performed by “technically competent” staff.
HSE outlines this advice its guide to warehouse health and safety, which we recommend that all warehouse owners read in full. Not following this advice, or not fully understanding it, can lead to some pallet racking dangers that you may not have even thought of.
Floor Safety: More Than Slips, Trips, And Falls
When most people think of floor safety, they think of yellow foldaway plastic signs saying “WET FLOOR” and gritted walkways. This kind of floor safety is important and it’s the subject of HSE’s INDG2255 “Preventing Slips and Trips at Work: A Brief Guide”.
However, with regards to storage systems, whether that’s pallet racking or cantilever racking, there are two other major kinds of floor-related danger. Firstly, there are uneven floors. HSE recommends that racking is installed on even flooring. Otherwise, the racking will be unbalanced even when there is no load. Secondly, there are weak floors. We don’t typically think of floors as “weak”, especially those on the ground floor.
However, it’s worth finding out what the maximum weight your floors can take is, how you can strengthen them, and where particular weaknesses in your floor might be. Your racking system might be able to handle a certain amount of weight but, if your floor can’t, you’re in a huge amount of danger.
Knowing exactly how and where to install your racking can be difficult for those without proper experience; this is why HSE recommends that it is done by “competent people”.
It then recommends installation training from the Storage Equipment Installers Registration Scheme (SEIRS), who are overseen by SEMA. Much like with racking inspection training and racking inspection frequency, HSE has its recommendations, but it is ultimately the warehouse owner’s decision to follow or not follow those recommendations.
In fact, this brings us to an important legal change that occurred with regards to HSE in 2015. It highlights yet another racking danger that the average employer might not be aware of.
Technically Competent and The 2015 CDM Regulations
“Competent” is a word HSE likes to use a lot in its guide to warehouse safety, and it’s a word which is intentionally vague. This because, since the introduction of the updated CDM regulations in 2015, it is ultimately the warehouse owner’s responsibility (the “client”) to maintain safety in their warehouse. In other words, a “competent” person is whoever a warehouse owner thinks a competent person is.
That said, HSE has its recommendations and, if the worst should happen and a warehouse owner was found flouting these recommendations, then that warehouse owner (that “client”) could be held legally responsible.
This change replaces HSE’s old system of enforcing its recommendations with inspectors. Moreover, according to Tony Mitchell from HSE, the previous system allowed anyone with a card to call themselves an “expert” or “technically competent” and, by the time the regulations were introduced, there were over 300 of these “card schemes”.
Nowadays, there is no enforcement and there are no cards. There are only HSE’s recommendations and the people who a client believes are “technically competent” or an “expert”. If an accident or a fatality happens and the recommendations weren’t followed, then there would be legal action. What is more, the client responsible for the accident would be expected to defend the “technically competent” people or “experts” who worked in their warehouse.
This change can be difficult to understand because it doesn’t change any of HSE’s advice. In fact, upon learning about the new CDM regulations, most employers will continue to act in the same way. However, the unexpected pallet racking danger that this brings with it is that a warehouse owner may have a very lax definition of “expert” or “technically competent”.
This reason, we recommend following HSE’s advice as closely as possible. For example, HSE recommends internal racking inspections by a “technically competent” person.
For this, consider racking inspection training from a SEMA approved racking inspector — an inspector which HSE labels an “expert” — in order to give your staff the technical competence they need.
Racking Inspection Frequency and Bad Lighting
Bad lighting is a much bigger problem for workplaces than most realise. Badly placed lighting fixtures can be troublesome for racking systems in particular for two reasons.
- They could be physically blocking the racking
- They do not light the racking system well enough
Avoiding the former danger is simply a matter of moving the lighting far enough away from the racking system or installing the racking system so that this is not an issue. Avoiding the latter danger can be slightly more difficult.
The correct racking inspection frequency for internal, staff-permed racking inspections is up to the warehouse owner. However, with bad lighting, it won’t matter how high this racking inspection frequency is. An expert SEMA approved racking inspector, knows exactly what to look for and where to find it. However, your staff will not be experienced enough to know if your racking is damaged under bad lighting — no matter how many times they inspect it.
To make your warehouse safer, you need to make sure that every part of your warehouse is well lit. This can be difficult and, as objects move around the warehouse and light bulbs fade, it changes. Still, as with all safety precautions, keeping your warehouse well-lit is a constant process.
Warehouse avoids these unexpected pallet racking dangers with a racking inspection by a SEMA approved inspector from SEE.