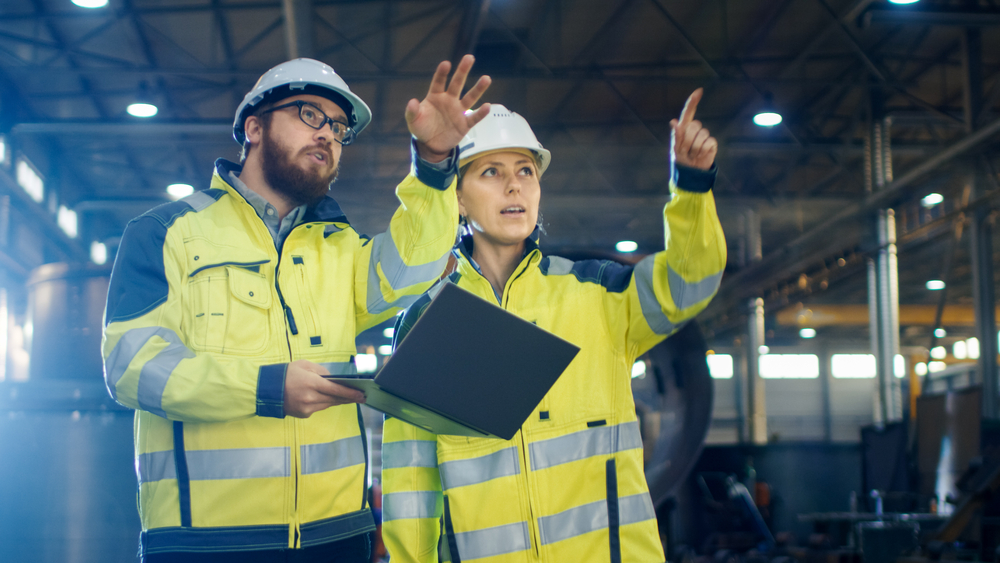
Warehouse safety requires discipline, but it also requires knowledge.
If you own a warehouse, keeping it safe can be hard. After all, warehouses are big buildings, which means there will be a myriad of different things to consider when you’re performing a risk assessment. To help you along the way, here are four top warehouse safety tips.
Warehouse Safety Tip #1: Use a Floor Map
You are legally required to perform a risk assessment if your business has more than five employees. If it has less, it’s still recommended, but you don’t need to write anything down. As such, “perform a risk assessment” isn’t so much a warehouse safety tip as it is something which you are legally obliged to do.
Floor maps, though, are different. You are not legally required to use them, but they are a great way of helping you specifically with spotting the risks that exist as a result of your flooring. Warehouse floor space can be enormous, so identifying where potential hazards are can be hard if you do it as part of your general risk assessment. By doing your risk assessment for your floor separately through using a floor plan, you can be sure that you don’t miss anything.
Warehouse Safety Tip #2: Invest in Training
According to the CDM Regulations 2015, the people who work in your warehouse need to be “competent”. This notion of “competence” is intended to replace the countless card schemes which existed prior the CDM Regulations 2015, and it comes with a shift in responsibilities from HSE to the “client”. The “client” is the person who runs a construction project or — in the case of warehouses — the person who owns the warehouse.
In summary, the CDM regulations mean that it’s up to the warehouse owner to decide whether or not someone is competent enough to work in their warehouse. If an accident should happen as a result of incompetence, the warehouse owner may be legally responsible.
This change in the onus of responsibility means that safety training is more important than ever. HSE won’t be there to make sure that your staff are trained, but the law will catch up with you if an untrained member of staff makes a dangerous mistake which a competent member of staff wouldn’t have.
Warehouse Safety Tip #3: Record Near Misses
Near misses are not accidents. Yet, they need to be treated as such because the only difference between an injury, a fatality and a near miss is luck. Every business needs a bit of luck when it comes to sales or marketing, but it’s not something which should ever be relied upon when it comes to safety. In fact, as a general rule, you should never rely on luck in business. Just be happy when it happens.
By recording near misses, you get to learn from a mistake without having to suffer the consequences of a mistake. By not recording or not acting upon near misses, you are willfully putting your employees in danger, and they may well have cause to make a legal complaint.
Warehouse safety tip #4: Nominate a person responsible for racking safety (PRRS)
One the one hand, safety is everybody’s responsibility. On the other hand, nominating a person responsible for racking safety (PRRS) guarantees that at least one person will consider the rack safety in your warehouse. This delegation can be done across the board — a person responsible for floor safety, a person responsible for vehicle safety, a person responsible for warehouse security.
Doing so will ensure that at least one person is paying attention to every aspect of warehouse safety at any given time. When combined with proper safety training, it will mean that you know that each responsible person is also a competent person.
For warehouse safety tips and a warehouse safety training course from a SEMA approved racking inspector, contact Storage Equipment Experts today for a FREE quote.