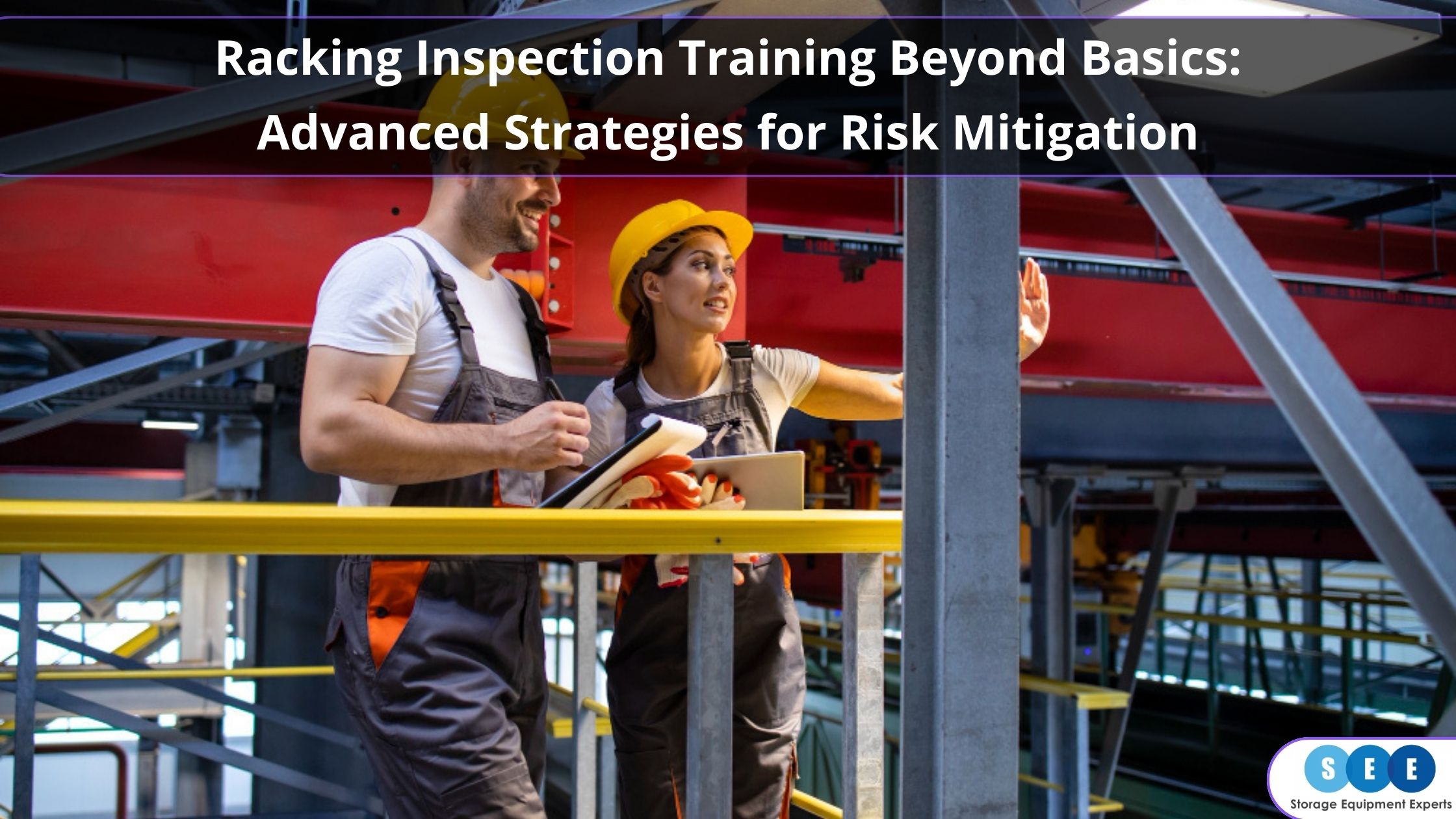
Warehouse safety is the most important aspect of warehouse management, with the integrity of racking systems playing a key role. Advanced training in racking inspection is an absolutely critical factor in pinpointing and mitigating potential hazards, thus safeguarding both personnel and inventory.
In this blog, we’ll shift the spotlight from elementary principles to more advanced strategies in racking inspection training, illustrating the importance of progressing from basic understanding to expert-level risk mitigation tactics.
The Bedrock of Racking Inspection Training
A robust grasp of racking inspection basics sets the stage for enhanced warehouse safety protocols. Initial training sessions arm inspectors with insights into typical vulnerabilities alongside skills for conducting comprehensive assessments.
Topics covered include:
- Structural components of racking systems
- Spotting wear or damage
- Adhering to regulatory compliance standards
This foundational knowledge is crucial for adopting more sophisticated inspection techniques – you can’t learn the advanced techniques without first learning the basics, after all.
Uncovering Hidden Risks
Advanced training should show you how to identify concealed hazards. Inspectors learn to:
Recognise Subtle Risk Factors
Advanced racking inspection training equips inspectors with the skills to detect risk factors that might not be immediately evident. These subtle indicators of potential problems can include deformations or other types of damage in racking components, irregularities in floor anchoring, or early signs of corrosion that, if left unchecked, could compromise the structural integrity of the entire system. Understanding what type, size & condition of pallets be stored onto the racking and how the pallets are stored correctly onto the racking.
Inspectors are taught to pay attention to:
- Minor shifts in the alignment of racks that could indicate foundation issues or uneven load distribution.
- Small cracks or bending in beam connectors which could lead to catastrophic failures under stress.
- Signs of wear in protective coatings which could expose the material to accelerated corrosion.
This more nuanced observation capability is critical for early intervention, preventing minor issues from escalating into significant hazards.
Understand Operational Impacts on System Integrity
The day-to-day operations within a warehouse can exert various stresses on racking systems. Advanced training from a SEMA-approved racking inspector goes into more detail on how different operational practices, such as the frequency and method of loading and unloading, can affect the durability and safety of these structures. For example, repeated impact from forklifts, overloading, or improper loading techniques can all gradually weaken the racking system.
Inspectors learn to:
- Assess the impact of operational workflows on racking stability and safety.
- Identify operational practices that may contribute to accelerated wear or potential system failure.
- Recommend adjustments in warehouse operations to mitigate these risks, ensuring the long-term integrity of the racking system.
Employ a Detailed Approach to Risk Detection
A detailed approach to risk detection involves a comprehensive examination of the racking system beyond what is visible at a glance. This thorough analysis includes checking for hidden defects that could undermine the racking’s performance or safety.
Advanced Training Emphasises:
- The importance of a regular inspection and how to complete a racking inspection.
- Systematic documentation of all findings for a historical record of the racking system’s condition which can be crucial for identifying patterns of wear or stress over time.
- A regular schedule of detailed inspections that covers every component of the racking system, from the floor anchors to the load beams, ensuring that no part of the system is overlooked.
Through these expanded skills and knowledge, inspectors are better equipped to identify and address risks, contributing significantly to the safety and efficiency of warehouse operations.
Structural Analysis of Racking Systems
Here, we introduce methods for an in-depth structural analysis of racking systems, crucial for foreseeing and circumventing possible failures. The training focuses on:
- Assessing load distribution and structural integrity
- Evaluating environmental impacts on racking systems
- Anticipating issues to bolster safety
Drafting Proactive Inspection Schedules
Switching to proactive inspection planning provides large reductions in system failure risks.
Discussion Points Include:
- Decide how often the inspections should be completed.
- Deciding who will complete the inspections and planning dates in advance.
- Unloading damaged racking when required to reduce risks of failure.
- Rectifying all concerns found during the inspection.
- Monitoring inspection reports for repetitive damage or other concerns.
Mastering Emergency Response
Even the most detailed and advanced racking inspections may not be enough – sometimes, issues are simply unavoidable. Advanced racking inspection training extends to emergency preparedness, highlighting rapid response and recovery techniques.
Key Areas Include:
- Implementing an effective reporting system so that all warehouse staff know how to report racking related concerns and who to report those concerns to
- Investigating racking related concerns immediately
- Taking action to manage any risks that racking concerns create
- Safely unload and close off racking to manage risks of racking failures
Building a Safety-First Culture
Advanced training underscores the importance of promoting a workplace ethos centred on safety and ongoing improvement.
Suggestions for cultivating this environment involve:
- Encouraging continuous education
- Engaging all staff in safety practices
Implementing Advanced Strategies
Adopting advanced risk mitigation strategies requires methodical planning. This guide outlines steps for transitioning to more sophisticated practices, ensuring a completely holistic approach to warehouse racking safety.
Advancing racking inspection training is vital for comprehensive risk mitigation and enhancing warehouse safety. Organizations can protect their workforce and assets by encouraging continuous learning and adopting more in-depth strategies, making advanced training an indispensable element in warehouse safety excellence.
For more insight into racking training or to arrange your own on-site training session, check out SEE Racking Inspections today.