Modern warehouses are designed to be hubs of efficiency where goods are stored, processed, and dispatched quickly and accurately. For all the thought and care that goes into their operational architecture, however, warehouses face a major, and often underestimated, fire risk: idle pallets.
These ubiquitous logistics components, whether they be wooden or plastic, are highly combustible, especially when piled high and dried out. Recognising this key vulnerability, the Fire Protection Association (FPA) has updated its technical bulletin, TB215: Sprinkler Protection of Idle Pallet Storage. More than just an amendment, this latest iteration (TB215:2024:1) is a fundamental re-evaluation of best practices in warehouse fire safety across the UK.
In this article, we’ll examine warehouse fire safety, explore the FPA’s new recommendations and take a look at why professional inspections by companies like SEE Racking Inspections are so important to the safety equation.
The Heightened Risk of Idle Pallet Storage
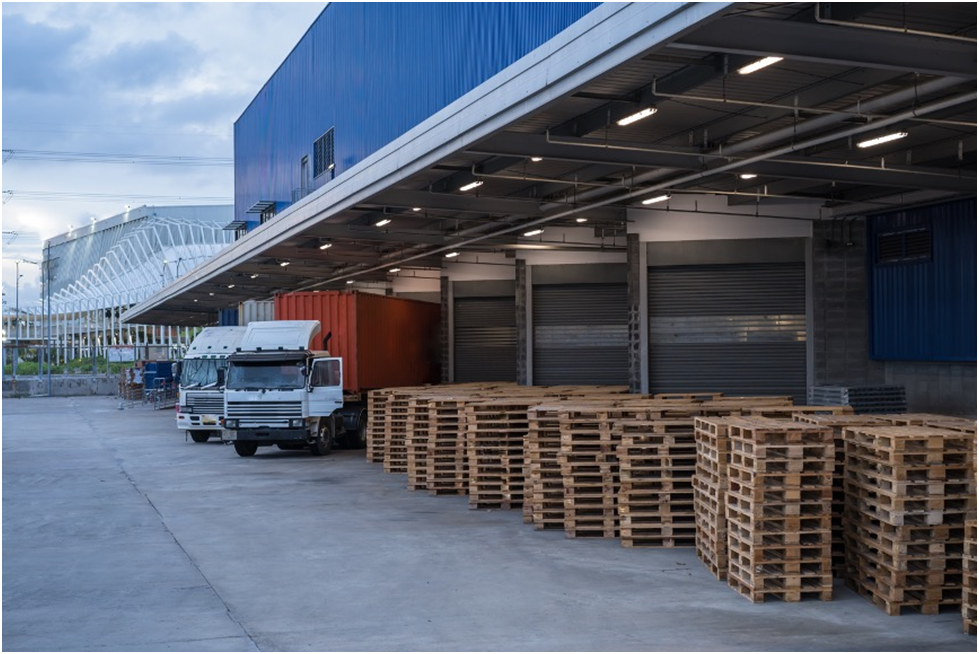
Warehouses, by their very nature, house vast quantities of goods, often packaged in combustible materials. While the primary safety focus often rests on the stored products themselves, the supporting infrastructure, particularly idle pallets, presents a major hazard.
These seemingly innocuous stacks can ignite with frightening speed and intensity, creating a fire that can rapidly overwhelm conventional suppression systems. The sheer volume of air trapped within pallet stacks acts as a natural accelerant, creating a chimney effect that fuels the flames.
The consequences of pallet fires extend far beyond the immediate storage area. Heat from burning pallets can be so intense that it compromises structural steel and concrete, potentially leading to building collapse. Adjacent structures, sometimes separated by what seemed like safe distances, have suffered severe damage from radiated heat alone.
Key Innovations in TB215:2024:1
In response to these risks, TB215:2024:1 introduces several major changes. At its core, the bulletin presents a more sophisticated approach to pallet material classification, allowing facility managers to make decisions based on specific fire behaviour characteristics rather than general material categories.
Instead of rigid, one-size-fits-all rules, the revised document provides scalable options that account for varying facility needs. Height limitations, design density requirements, and storage configurations now follow a more nuanced approach, with different storage configurations requiring different protection strategies.
Improved Pallet Material Classification System
TB215:2024:1 goes beyond simple wood versus plastic pallet categorisations. The bulletin’s updated classification system thoroughly examines various pallet materials, analyzing how different compositions behave under fire conditions. Traditional timber pallets now have subcategories based on treatment methods and moisture content, while plastic pallets are evaluated based on their specific polymer compositions.
The introduction of hybrid and composite pallet classifications is a fundamental advance in thinking. These increasingly common materials, which might combine wood products with synthetic reinforcements or fire-resistant coatings, require special consideration. The bulletin provides detailed guidance on how these modern materials perform in fire conditions, helping warehouse operators make more effective decisions about their storage requirements.
What’s more, a standardised testing methodology underpins the entire classification system. This gives pallet manufacturers clear benchmarks for product development while providing warehouse operators with reliable metrics for comparing different pallet options. The result is a more scientific approach to pallet selection that considers both operational needs and fire safety requirements.
Advanced Storage Arrangement Guidelines
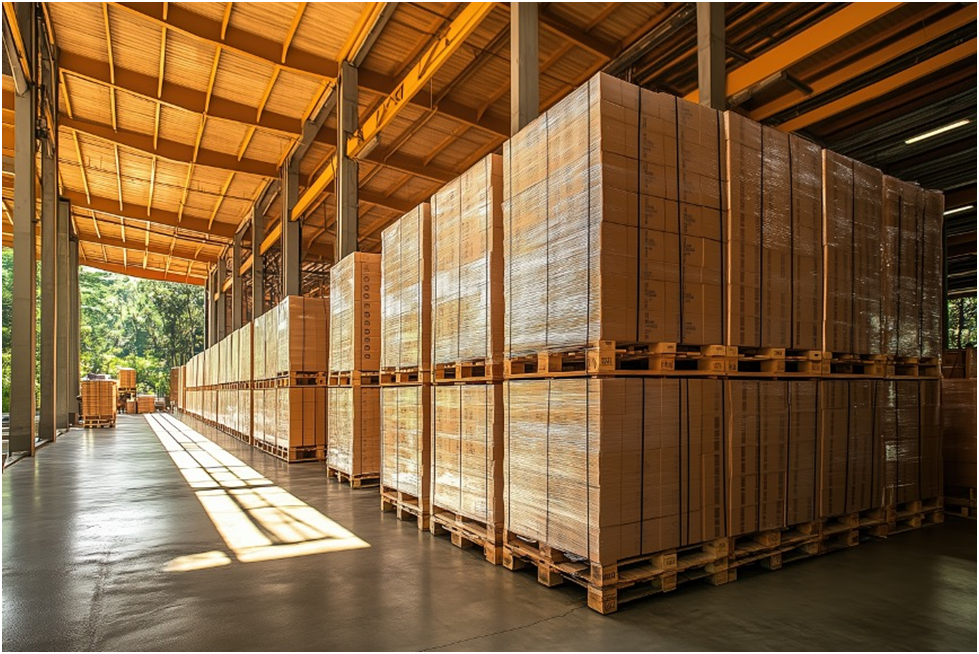
Space is the main economic resource in warehouses, and TB215:2024:1 addresses this business reality by providing precise spacing requirements between pallet stacks. These measurements are not arbitrary – they’re based on extensive research into fire spread patterns and the effectiveness of various intervention methods.
The bulletin takes a three-dimensional approach to storage configuration. Beyond simple stack heights and aisle widths, it considers how different arrangement patterns affect fire development and suppression effectiveness. Solid pile storage, rack storage, and temporary staging areas each receive specific attention, with guidelines tailored to their specific characteristics.
Within this, storage height limitations have been redefined. Instead of blanket restrictions, the new guidelines offer a range of options based on available fire suppression systems, facility characteristics and appropriate safety margins. This flexibility allows warehouses to maximise storage density while maintaining appropriate safety margins.
Breaking with traditional approaches, TB215:2024:1 also introduces the concept of strategic fire breaks within large pallet storage areas. These designated spaces serve as natural barriers to fire spread while providing access points for firefighting personnel. The guidelines include specific calculations for determining optimal break locations based on storage volume and facility layout.
More Stringent Sprinkler System Requirements
At the heart of modern warehouse fire protection is the sprinkler system, with the bulletin setting new standards for these installations. The revised specifications for sprinkler head selection exceed simple temperature ratings, addressing response times and coverage patterns specifically engineered for pallet storage scenarios.
Water supply requirements receive particular attention in the update. When examining real-world fire events, the bulletin establishes minimum thresholds for water volume, pressure and duration. These specifications make sure that suppression systems can maintain effective operation throughout extended fires, even when dealing with the intense heat that characterises pallet fires.
The bulletin additionally focuses on the benefits offered by Early Suppression Fast Response (ESFR) systems. These advanced systems, when properly specified and installed, can dramatically improve fire control capabilities. The guidelines provide detailed parameters for ESFR implementation, including specific requirements for ceiling height, storage configuration, and water supply infrastructure.
The positioning of sprinkler heads also takes on specific new importance. Rather than relying on standard spacing patterns, the bulletin introduces configuration-specific requirements that account for pallet stack arrangements and potential fire development patterns. It’s a targeted approach that helps minimise water damage while maximising suppression effectiveness.
Implementation Strategies for Warehouse Managers
Making the transition to TB215:2024:1 standards doesn’t have to disrupt warehouse operations. The bulletin provides a practical roadmap for implementation, allowing facilities to phase in improvements while maintaining productivity. This systematic approach helps managers prioritise upgrades based on risk levels and available resources.
Support for implementation extends beyond the bulletin itself. The FPA has developed a comprehensive resource library, accessible through their website, that includes detailed technical specifications, case studies, and best practice guides.
Creating a safer future for warehouses
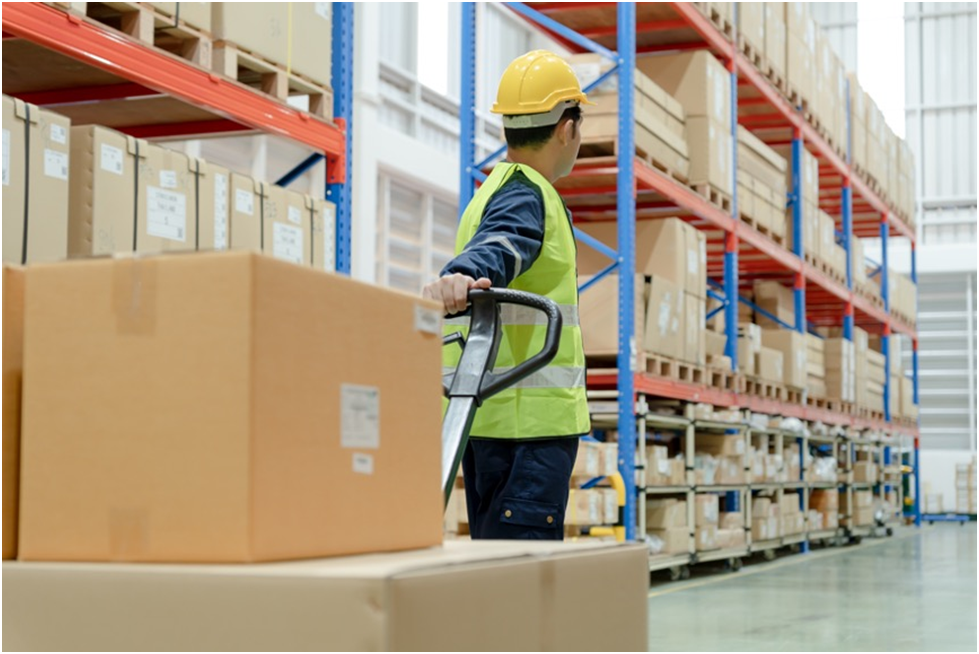
The FPA’s TB215:2024:1 marks a major step forward in warehouse fire safety, with the update’s best practices helping businesses protect lives and physical assets, as well as maintain industry compliance.
As UK-wide specialists in pallet safety, SEE Racking Inspections offers independent, third-party storage inspections conducted by SEMA-approved and SARI inspectors. Our comprehensive services make sure your racking systems are operated in the safest way possible, minimizing risk and helping businesses meet their corporate safety obligations. In conjunction with the FPA’s new guidelines, SEE Racking Inspections delivers businesses a dependable way to improve both warehouse safety and business performance.