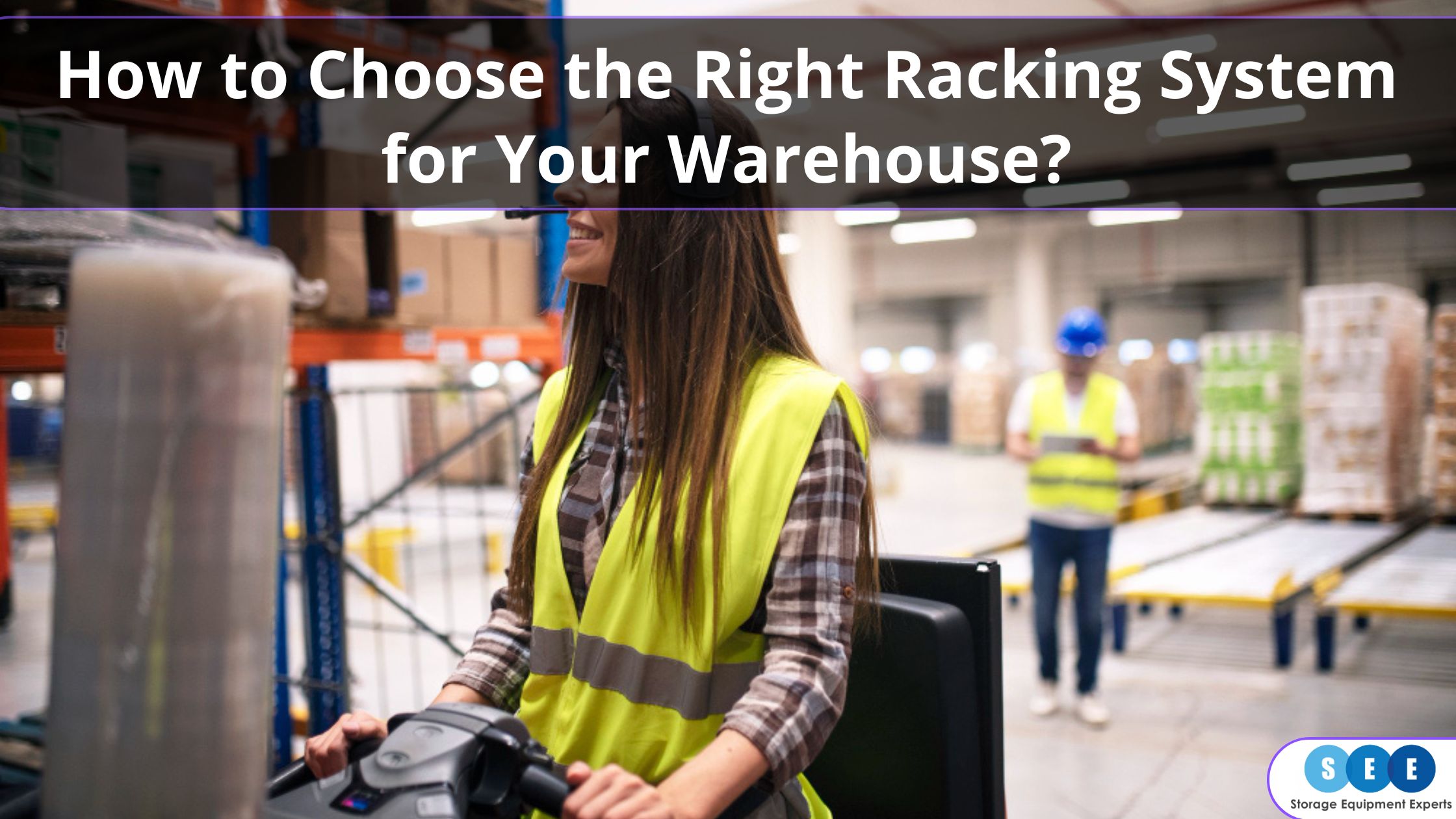
Selecting the right racking system for your warehouse is a key decision that directly impacts your operational efficiency, storage capacity, and overall workflow. With a variety of racking systems available, each designed to meet specific needs, understanding your options and their benefits is the only way to ensure you’re making the best choice.
In this article, we’ll guide you through the essential factors to consider when choosing a racking system that perfectly aligns with your warehouse requirements.
Understanding your storage needs
Before you can choose the right warehouse racking system, you need a clear understanding of your storage needs.
Consider the following questions:
- What types of products do you store? Whether you’re storing pallets, cartons, or long, bulky items, the nature of your inventory will heavily influence your racking choice.
- How often do you need to access stored items? High-turnover items require a system that allows for easy and frequent access, while long-term storage prioritises maximum space utilisation.
- What are the dimensions and weight of your inventory? Ensure that the racking system can accommodate the weight and size of your goods without compromising safety.
Types of Industrial Racking Systems
Understanding the different types of racking systems available will help you match the right solution to your warehouse needs.
Selective Pallet Racking System
Features:
- Accessibility: Provides direct access to every pallet, making it ideal for high-turnover products.
- Versatility: Can be adjusted to fit different pallet sizes and weights.
Best For:
- Warehouses with a wide range of products that require frequent access.
- Operations that prioritise versatility and ease of use.
Drive-In/Drive-Through Racking System
Features:
- High-Density Storage: Allows forklifts to drive directly into the racking system, maximising storage space.
- Limited Access: Best suited for storing large quantities of the same product.
Best For:
- Warehouses with large volumes of similar products that don’t require frequent access.
- Facilities looking to maximise space utilisation with minimal aisles.
Push-Back Racking System
Features:
- Last-In, First-Out (LIFO) Storage: Pallets are loaded and unloaded from the front, with subsequent pallets pushing previous ones back.
- Space Efficiency: Offers high-density storage without sacrificing accessibility.
Best For:
- Operations that require efficient space usage and can accommodate LIFO storage.
- Warehouses with limited floor space but high inventory turnover.
Cantilever Racking System
Features:
- Specialised Storage: Designed for long, bulky items like lumber, pipes, and metal beams.
- Adjustable Arms: Can be customised to fit various product lengths.
Best For:
- Warehouses that need to store long, unwieldy items that don’t fit standard pallet racking.
- Operations requiring flexible storage solutions for oversized products.
Pallet Flow Racking System
Features:
- First-In, First-Out (FIFO) Storage: Pallets are loaded from one side and retrieved from the other, ensuring the oldest stock is used first.
- Gravity-Fed System: Uses inclined rollers or wheels to move pallets forward automatically.
Best For:
- Warehouses with a high turnover of perishable or time-sensitive goods.
- Operations that prioritise FIFO inventory management.
Space optimisation and layout design
Choosing the right racking system is only part of the equation. Optimising your warehouse space and layout will greatly affect overall efficiency.
Consider these factors:
- Aisle Width: Determine the appropriate aisle width based on your racking system and the type of forklifts or material handling equipment used.
- Vertical Space: Maximize the use of vertical space by choosing racking systems that extend to the ceiling, provided it remains safe and accessible.
- Flow of Operations: Design the layout to minimise travel time and streamline the movement of goods from storage to shipment.
When designing the layout, you can use computer-aided design (CAD) tools to create detailed floor plans and visualise different racking configurations. Make sure that you designate areas for staging, packing, and equipment storage to keep aisles clear and reduce the risk of accidents, and have one eye on the future: choose a layout that allows for flexibility and expansion as your storage needs grow.
Safety and compliance considerations
Safety should always be a top priority when selecting a racking system. Ensuring compliance with industry standards and regulations is not just about avoiding penalties but protecting your employees and inventory.
Key Safety Considerations
- Never exceed the recommended load capacity of your racking system. Ensure all employees are aware of these limits.
- Regularly inspect racking systems for signs of wear, damage, or overloading. Address issues immediately to prevent accidents.
- Ensure that warehouse racking systems are installed by professionals who understand the specifications and safety requirements.
Compliance Requirements
- Familiarise yourself with relevant industry standards, such as those provided by the Storage Equipment Manufacturers Association (SEMA) or Health and Safety Executive (HSE)
- Provide ongoing safety training for all employees who interact with racking systems to ensure they understand how to work safely and effectively.
Cost considerations and ROI
While cost is always a factor in any business decision, it’s important to look beyond the initial price tag when selecting a racking system. Consider the long-term return on investment (ROI) and how the system will contribute to your warehouse’s overall efficiency and profitability.
Cost factors to consider include the upfront cost of the racking system, installation and any necessary modifications to your warehouse, as well as the long-term maintenance costs associated with each type of racking system. Lastly, bear in mind that a more expensive system that optimises space better might offer greater ROI by increasing storage capacity and reducing operational costs.
Calculating ROI
- Assess how the racking system will improve workflow, reduce handling time, and increase overall productivity.
- Invest in high-quality systems that offer durability and require less frequent replacement or repair.
- Consider whether the system can adapt to future changes in inventory size or warehouse layout, adding value over time.
Making the final decision
With all these factors in mind, making the final decision involves weighing the pros and cons of each racking system against your specific warehouse needs.
Ideally, you should consult with experts. Seeking advice from warehouse design experts or racking system suppliers will ensure you’re making an informed decision. If possible, pilot a small section of the racking system to see how it integrates with your existing operations before committing to a full installation.
The right pallet racking systems can significantly enhance your warehouse’s efficiency, safety, and overall productivity. You can make a well-informed decision that benefits your business in the long run simply by carefully considering your storage needs, understanding the different types of racking systems, and factoring in space optimisation, safety, and cost.