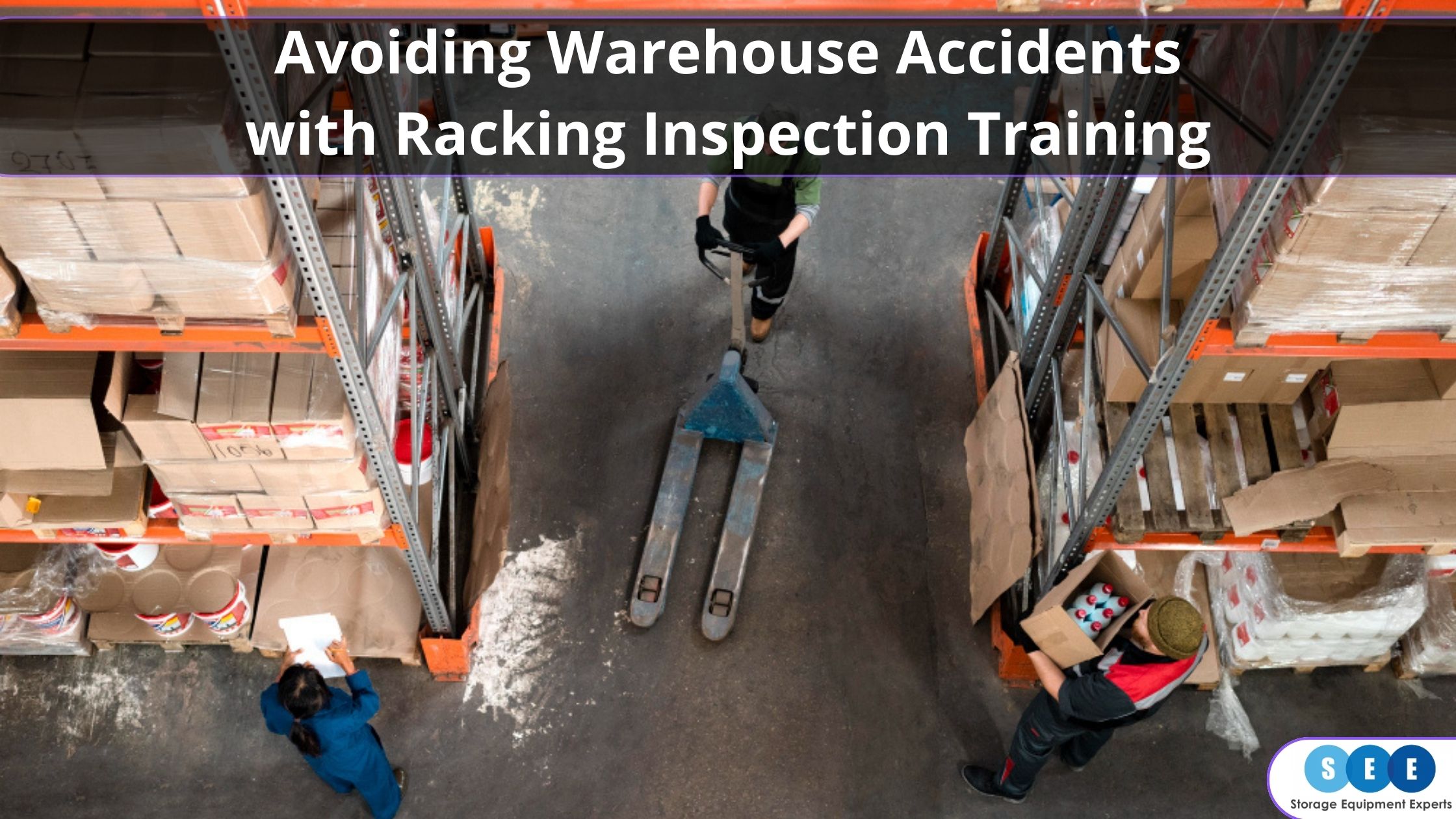
The safety and integrity of racking systems are at the very centre of good warehouse management. These structures, often towering and laden with significant weight, are the backbone of efficient warehouse operations – but if used incorrectly or poorly maintained, they can be highly dangerous and costly.
Ensuring the stability and safety of your racking through regular inspections is often thought of as tedious red tape or a procedural formality; in reality, it’s a fundamental aspect of operational safety.
The actual process of pallet racking inspection is complex as there are numerous areas that can be overlooked, with the potential for dire consequences.
This blog provides an overview of these common inspection errors and emphasizes the impact that comprehensive training can have in averting potential disasters – by understanding (and avoiding) these pitfalls, warehouse managers can take meaningful steps toward safeguarding their operations and workforce.
What is a Warehouse Racking Inspection?
Warehouse racking systems are typically in near-constant use, carry considerable weight, and are subject to frequent pushing and pulling as loads are dropped off or picked. This will inevitably lead to considerable wear and tear – even though these systems are built for strength and longevity, they will still need to be checked over every now and again to make sure they are in good shape. Regular racking inspections will identify potential issues before they escalate into serious problems.
Avoiding these inspections (or not conducting them properly) is not an option. The best-case scenario in a racking collapse is that stock is damaged, but the more likely outcome involves damages to equipment and injuries to personnel – clearly, anything you can do to avoid such an event should be prioritised.
If you are a warehouse manager or safety officer, you should start thinking about racking inspections as your first line of defence against potential hazards. Ensuring that your racking is regularly and thoroughly inspected means that the warehouse will generally be a safer and more efficient work environment – it’s a safeguard for employees, products, and business operations.
What are Common Racking Inspection Mistakes?
When it comes to racking inspections, several common mistakes can significantly compromise warehouse safety. One of the most frequent errors is overlooking damage or signs of wear – small dents, rust patches, bends or slight deformations might seem inconsequential but can dramatically reduce the structural integrity of the racks. This oversight is often due to a lack of detailed knowledge or underestimating the impact of minor damage.
A racking inspection should include checks to ensure that the racking system has not been altered from its original design which can include adding, removing or repositioning the horizontal beams. Check that pallets are stored correctly onto the system, that stored pallets are the correct size and type and that the pallets are free from damage.
Another frequent error is misjudging (or, even worse, ignoring) load capacities. Racking systems are designed to support specific weight limits, and overloading them can lead to structural failures. Inspectors might not always check for changes in load distribution or recognize when a rack is being overburdened, leading to dangerous conditions.
Finally, every racking inspection should be followed by actions to rectify and concerns. The inspection should be recorded on paper or digitally and these records should be kept on file for future reference. Incomplete or inaccurate records of inspections can lead to a lack of accountability and follow-up, and this lapse can mean that identified issues are not addressed promptly, increasing the risk of accidents.
Each of these mistakes, while seemingly small, can lead to significant safety risks. The accumulation of these oversights can create a hazardous environment, endangering both employees and the stored goods and potentially leading to catastrophic outcomes.
Importance of Training in Racking Inspections
Proper racking inspection training is essential for ensuring warehouse safety and operational efficiency – a badly performed inspection can actually be worse than no inspection at all, as it will lead to a false sense of security. Proper training equips inspectors with a deep understanding of the complexities involved in racking systems and enables them to identify potential risks that untrained eyes might miss.
The gold standard for racking safety is SEMA – the Storage Equipment Manufacturers Association. This is the industry body that is dedicated to ensuring that racking safety is prioritized and that there are best practices available for warehouse operators and managers to adhere to.
The best approach for you is to make sure that any racking inspection training that you implement is carried out by approved SEMA racking inspectors. This will ensure that your training meets the industry-agreed best practices and guidelines.
The training program should also cover different racking systems, including their design, load-bearing capacities, and the impacts of various environmental factors. Trainee inspectors have to learn about the early signs of damage or wear and how to spot immediate concerns – as well as anticipate potential future issues.
High-quality training will also place an emphasis on the importance of accurate and thorough documentation. It teaches inspectors how to record their findings effectively (racking inspection checklist (add a link to our racking inspection checklist), ensuring that any identified issues are clearly communicated and addressed promptly – this aspect of training is crucial in establishing a reliable process for follow-up actions and accountability.
The value of training extends beyond the technical aspects. It also covers adherence to safety standards and regulations, which is vital for legal compliance and maintaining a safe work environment. Having a good understanding of these standards means that inspectors can ensure that the racking systems meet all required safety criteria.
Training gives inspectors the knowledge and skills necessary to conduct thorough and effective inspections – it is this expertise that will be key to avoiding the common mistakes that can lead to warehouse disasters.
What Does Racking Inspection Training Consist Of?
Training will ideally take place at your site – this provides the opportunity to carry out a practical session in your warehouse and is the best way to ensure that the course is tailored to your precise needs (including the type of racking you use, for example).
Attendees should include as many people as you can spare but should prioritize those that use materials handling equipment like forklifts and pallet trucks, as these are the people most likely to cause accidental damage to the racking (and therefore be well placed to identify and report it).
Racking inspection training is typically a one-day course, and with SEE Racking Inspections will result in the receipt of a certificate showing completion and that the newly-trained inspector has the skills to complete internal inspections.