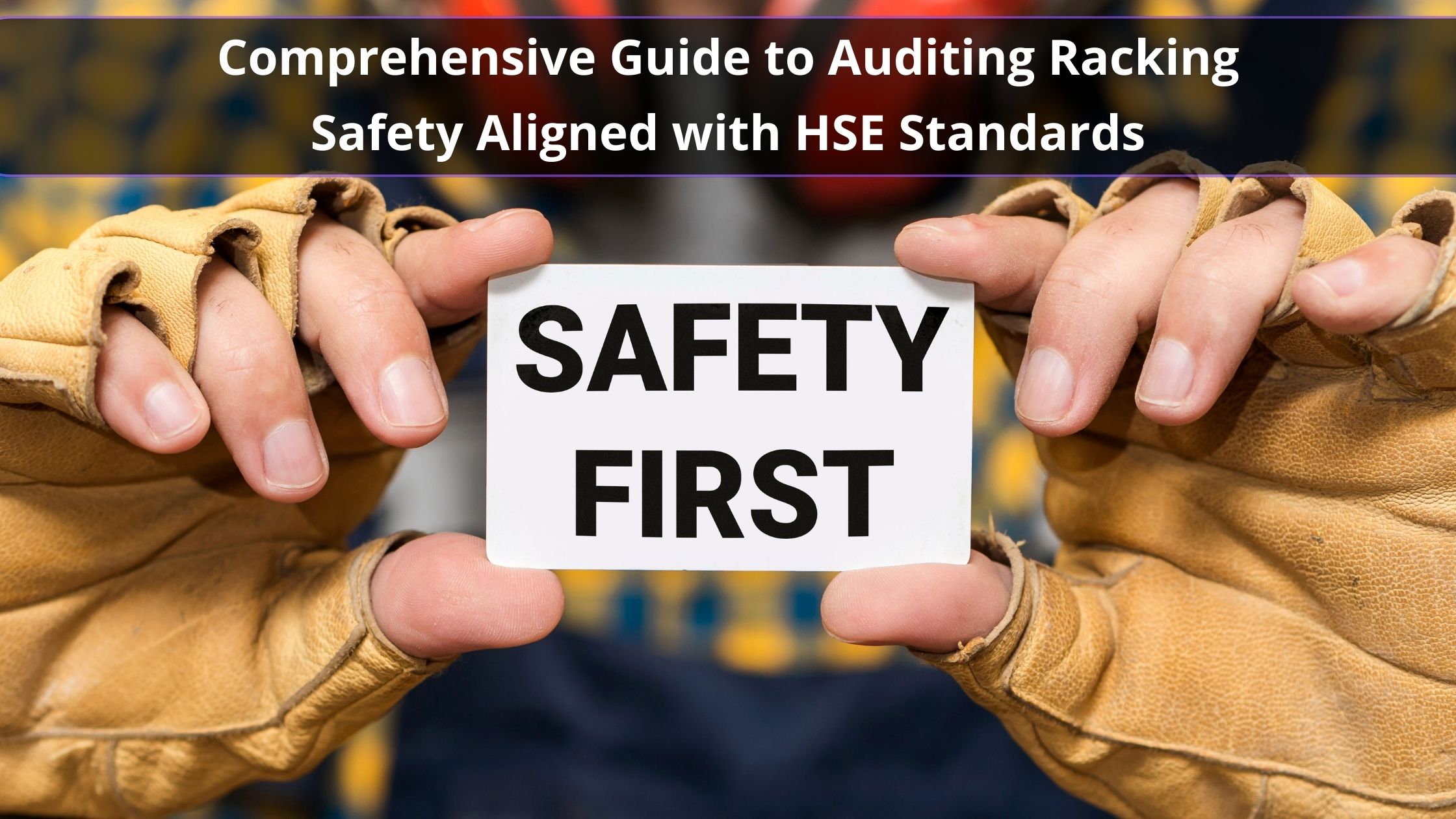
In the bustling ecosystem of a hse warehouse, every component plays a pivotal role in maintaining harmony and efficiency. Central to this are the racking systems – skeletal structures that bear the weight of products and the expectations of a smooth supply chain.
The strength of your racking can be compromised over time, though, and even the smallest damage can domino into significant safety issues.
The Health and Safety Executive (HSE) has published precise guidelines, emphasising the delicate nature of racking materials and the importance of regular safety audits. In this guide, we’ll take a look at the step-by-step processes that keep racking systems in check, safeguarding both human resources and inventory.
Read on for everything you need to know.
Preliminary Racking Inspection Preparations
Every warehouse needs to assign a dedicated ‘person responsible for racking safety’ (PRRS). This individual looks at everything to do with racking safety – from the operational frequency, equipment used, warehouse dimensions, and even the proficiency of personnel, to pinpoint potential threats to the racking structure.
As the first step of the inspection process, the PRRS should:
- Assemble a safety audit team – Highlight the importance of having a multidisciplinary team, including safety officers, warehouse managers, and maintenance personnel.
- Gather necessary tools – Racking inspection checklists, safety manuals, protective gear, and measuring tools.
The Different Types of Racking Inspections
Understanding the depth and frequency of racking inspections is essential for maintaining warehouse safety. In HSG76, the HSE emphasizes a tiered approach to these inspections, ensuring that potential issues are identified and rectified as soon as possible.
Immediate Reporting
A culture of ‘immediate response’ must be nurtured across the warehouse – should any employee, irrespective of their designation, notice a safety issue or damage, it’s their responsibility to report it instantly to the PRRS. Swift action can preempt larger problems, and having systems in place for such immediate reporting creates a safety-conscious environment.
Visual Inspections
These are the frequent, more general checks that ensure the daily safety of operations. The PRRS should oversee inspections at weekly or other regular intervals determined by a risk assessment – it’s a proactive approach, capturing any noticeable issues before they escalate, with every check documented formally.
Expert Inspections
This level of inspection delves deeper. These inspections, which should be done at least annually by a technically competent individual, result in a detailed written report submitted to the PRRS. Their findings help strategize remedial actions, ensuring the longevity and safety of the racking systems. Make sure that the inspector you choose is a qualified expert by always using a SEMA-approved racking inspector.
In essence, this hierarchical structure ensures a holistic surveillance of the racking systems, leaving no room for oversight.
Steps in the Racking Safety Audit Process
Safety in a warehouse setting isn’t merely about following protocols but ensuring that every piece of equipment, especially the racking systems, is in optimum condition. Given the importance of this, a rigorous safety audit process for your racking systems is mandatory. Here’s a comprehensive guide to understanding this audit process:
Visual Inspection
A visual once-over can reveal a lot more than you’d anticipate – look out for obvious signs such as damage such as dents or bends to any of the components within the racking structure, look out for damage to pallets, unstable loads on pallets or pallets that are too heavy or too big/small to be stored safely onto the racking and take note of anything else that doesn’t look right. Often, it’s these visual cues that provide the first hint of potential issues.
Load Checks
Overloading or unevenly distributed weight is a precursor to many racking mishaps. Each shelf within a racking system has a specified weight limit – exceeding this poses risks. It’s crucial to ensure that every shelf’s load is within this designated limit and that the weight is spread out evenly, preventing undue stress on any specific section.
Alignment and Anchoring
A misaligned rack, can compromise the entire system’s stability and it’s essential to confirm that all racks are vertical to within the SEMA limits. Additionally, the anchoring of these racks to the warehouse floor is of utmost importance to reduce the risk of them moving out of position& becoming misaligned or more importantly, being knocked over by accidental forklift impacts.
Accessibility and Aisle Width
Efficiency in a warehouse is as much about movement as it is about storage. Ensuring that the aisles between racking systems are sufficiently wide for machinery like forklifts is essential. These pathways need to be free from any obstructions, enabling smooth operations and reducing the risk of accidental impacts.
Safety Equipment Inspection
Beyond the racks themselves, the safety equipment associated with them is a critical component of the system. Safety pins, locks, beam safety clips, and other protective gear need regular checks to ensure they’re correctly installed and free from damage
Documentation Review
History tends to repeat itself unless we learn from it. Delving into maintenance logs, past inspection reports, and other relevant documentation should shed light on patterns or recurrent issues, allowing for proactive measures rather than reactive solutions.
Understanding HSE Standards for Racking Inspections
The Health and Safety Executive (HSE) sets the gold standard for racking safety, laying down guidelines that act as the North Star for warehouses globally. The HSE’s guidelines detail everything from the frequency of inspections to the types of checks necessary for different racking systems. Adherence to these standards isn’t just about ticking boxes – it’s about ensuring the well-being of employees and the safety of stored goods.
In the hustle and bustle of warehouse operations, a mishap can have dire consequences, both in terms of human safety and business implications. Maintaining compliance with HSE standards minimizes these risks, reinforcing trust and operational efficiency.
Post-Audit Actions
Once the audit concludes, the process isn’t over – the findings, irrespective of their nature, need to be meticulously documented. This record acts as a roadmap, helping prioritize repairs or modifications. Some issues might demand immediate attention, while others could be part of a routine maintenance schedule. Equally essential is communicating these results to all relevant stakeholders, as this transparency ensures that everyone is on the same page, working cohesively towards a safer workspace.
Regular Maintenance and Continuous Safety Checks
Safety isn’t a one-time effort – it’s a continuous commitment. Regular maintenance and periodic checks between comprehensive audits are paramount to uphold a consistently safe environment.
SEE Racking Inspections
Warehouse safety, especially when it concerns racking systems, is an intricate dance of regular inspections and preventive measures such as racking inspection training. With the HSE laying down the foundation for best practices, the responsibility is on businesses to incorporate these into their day-to-day operations. Every audit conducted, every flaw rectified, and every maintenance check contributes significantly to the long-term safety and efficiency of warehouse operations.
Ensuring racking safety is not a solitary endeavour – expertise and guidance play crucial roles. For those aiming for excellence in warehouse safety, seeking the expertise of seasoned professionals is a wise move. At SEE Racking Inspections, we don’t just offer inspections – we provide peace of mind.
In the world of warehousing, safety isn’t just a priority – it’s a necessity. Take a proactive step today and check out the comprehensive services offered by SEE Racking Inspections.