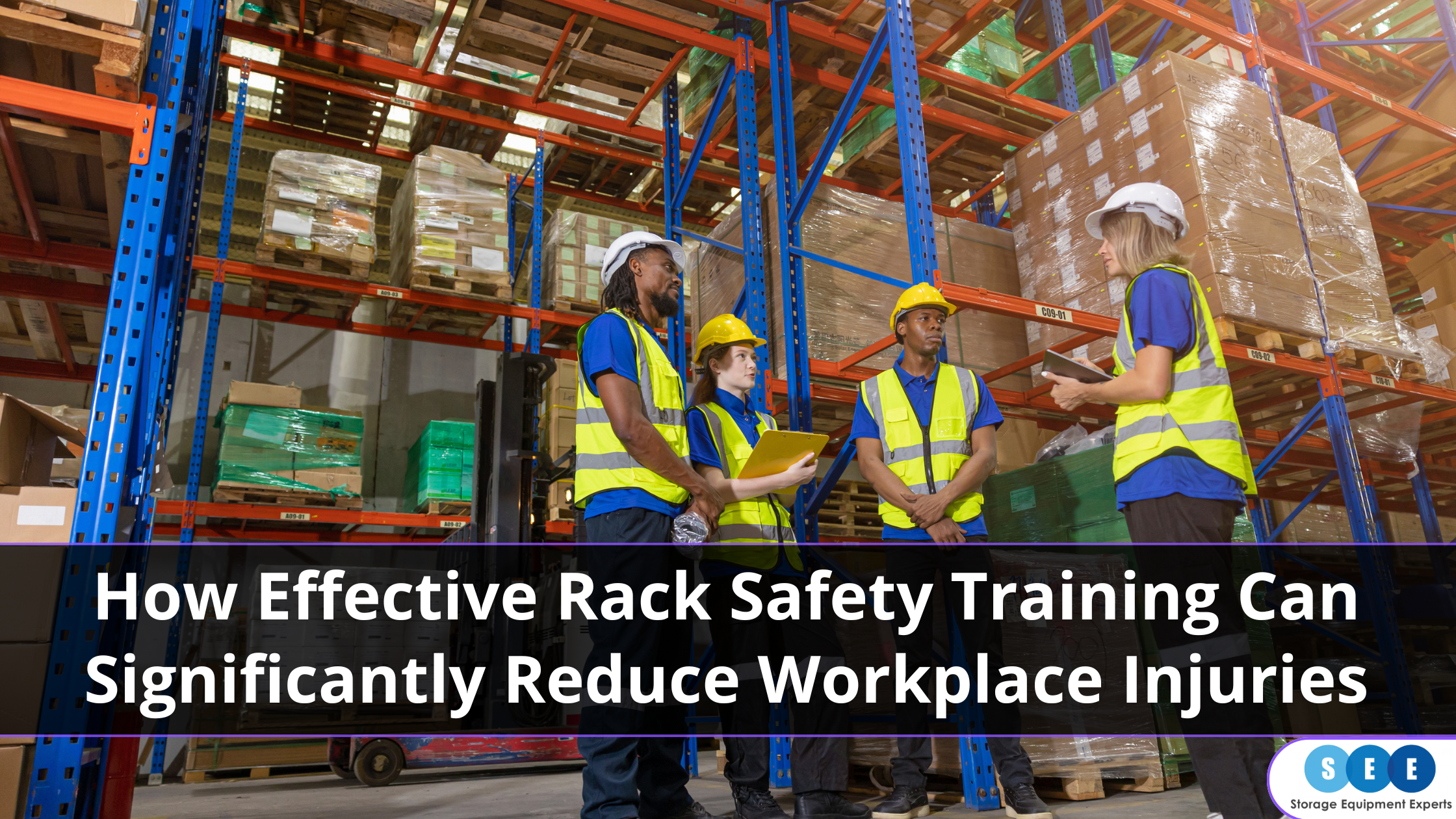
Rack safety training is an indispensable part of maintaining a safe and productive warehouse environment. Without the proper training, employees are at risk of injuries caused by the improper handling or overloading of warehouse racking systems.
This article will explore how proper rack safety training can lead to a safer workplace and lower the likelihood of injuries – bear in mind, though, that effective training doesn’t just prevent accidents. The benefits extend to smoother operations, reduced downtime, and happier, more productive workers.
1. Understanding the Importance of Rack Safety Training
Racking systems in warehouses hold heavy loads and are often stacked high, so (of course), any mistake in handling, loading, or maintaining these systems can lead to severe accidents. Rack safety training is essential because it:
- Reduces Accident Risks: Employees learn how to handle racking systems safely, minimising accidents caused by improper techniques.
- Protects the Workforce: A safe workplace is a productive one. Training empowers employees with the knowledge to protect themselves and their coworkers.
- Prevents Costly Damages: Safety training reduces the risk of damaged goods and racks, saving the company money in the long run.
- Ensures Compliance: Warehouses need to adhere to the Health and Safety Executive (HSE) safety standards. Proper training helps maintain compliance with regulatory guidelines.
Companies that prioritise rack safety training are protecting their employees as well as safeguarding their assets and reputation.
2. Key Areas of Focus in Rack Safety Training
Effective rack safety training covers a range of topics, each crucial for ensuring a safe work environment. Here are the primary areas of focus:
Load Capacity and Weight Distribution
Improper loading and weight distribution are common causes of rack failures. Employees need to understand:
- Weight Limits: Every racking system has a maximum load capacity. Training ensures employees know these limits and don’t exceed them.
- Even Weight Distribution: Improperly distributed loads can make racks unstable. Training should cover how to balance loads effectively to prevent tipping or bending.
Rack Inspection and Maintenance
Regular inspection and maintenance are key to preventing accidents. Training should emphasise:
- Daily Visual Checks: Employees should know how to conduct quick daily checks to spot any visible damage or misalignment.
- Scheduled Maintenance: Routine maintenance keeps racks in top shape. Employees should understand the importance of scheduled racking inspections and repairs.
Safe Equipment Handling
Forklifts and other heavy machinery are often involved in loading and unloading racking systems. Training should include:
- Forklift Operation Near Racks: Employees must learn how to operate forklifts safely around racking systems to avoid accidental impacts.
- Proper Loading and Unloading Techniques: Ensuring loads are placed and removed without causing strain or damage to the racks.
Emergency Procedures
In case of an accident, every second counts. Training employees in emergency response can significantly reduce injuries. This includes:
- Evacuation Procedures: Clear guidance on how to evacuate the area safely in case of a rack collapse.
- Reporting Mechanisms: Employees should know how to report any damage or potential hazards immediately.
Rack safety training that covers these areas provides employees with a comprehensive understanding of how to maintain a safe working environment.
3. Benefits of Rack Safety Training on Workplace Injuries
The positive impact of rack safety training extends beyond compliance and regulatory adherence. Here’s how it directly reduces workplace injuries:
Improved Hazard Awareness
When employees are well-trained, they become more vigilant in identifying potential hazards. For example:
- Spotting Structural Issues Early: Employees trained to recognise signs of damage – such as bent beams or other damaged to racking components – can report issues before they become major problems.
- Recognising Overloaded Racks: Training helps employees understand the dangers of overloaded racks so they’re more likely to catch these issues and prevent accidents.
Enhanced Confidence and Morale
Training gives employees the self-assurance to handle racks safely, leading to:
- Increased Confidence: When employees feel knowledgeable about safety, they are more likely to perform their tasks with precision and care.
- Higher Morale: A safe work environment boosts morale, as employees feel valued and protected. This creates a culture where safety is a shared responsibility.
Fewer Equipment-Related Accidents
Proper training minimises the likelihood of equipment-related accidents by ensuring employees know how to operate machinery safely around racks. Benefits include:
- Reduced Collisions: Employees learn how to manoeuvre forklifts and other equipment safely, reducing the risk of accidental impacts with racking systems.
- Efficient Loading and Unloading: Proper technique in handling equipment around racks minimises the chances of racks being destabilised or damaged during loading and unloading.
Lower Rates of Musculoskeletal Injuries
Incorrect lifting and loading practices can lead to musculoskeletal injuries. Safety training should include guidance on ergonomics, which helps:
- Prevent Strains and Sprains: Teaching employees safe lifting techniques reduces the risk of back injuries and other strains.
- Promote Correct Posture: Proper body mechanics help prevent injuries associated with repetitive lifting or awkward positions.
With fewer injuries, companies experience lower absenteeism and better productivity.
4. Creating a culture of safety
Rack safety training is most effective when it’s part of a larger culture of safety. Building this culture requires commitment from every level of the organisation.
Leadership Involvement
Employees are more likely to follow suit when management is committed to safety. Ways to demonstrate leadership involvement include modelling safe behaviour (managers should follow the same safety protocols as employees) and encouraging open communication. Employees should feel comfortable reporting any issues or hazards without fear of reprisal.
Rewarding Safe Practices
Incentivising safe behaviour encourages employees to prioritise safety. Consider implementing a safety rewards program to recognise employees who consistently follow safety protocols with rewards or recognition. You can also celebrate safety milestones, like acknowledging days without incidents or achievements in safety compliance, to encourage a safety-focused mindset.
Providing Ongoing Resources
Empower employees with the resources they need to maintain a safe environment. Useful resources might include:
- Safety Checklists: Provide checklists for daily, weekly, and monthly safety checks.
- Regular Updates: Share information about any updates to safety procedures, new equipment, or relevant industry standards.
You can create a workplace where rack safety training is valued, understood, and consistently applied simply by making safety a core part of your company’s values.
Conclusion
Effective rack safety training is a powerful tool in reducing workplace injuries. Training equips employees with the knowledge they need to work safely, as well as improves hazard awareness, builds confidence, and promotes proper handling techniques – all of which contribute to a safer work environment.
Investing in regular and thorough rack safety training programs is an investment in the well-being of your workforce and the smooth operation of your warehouse. Prioritising safety through effective training programs protects employees and strengthens your business’s efficiency and reputation. Find our more by checking out the SEE Racking Inspections blog today.