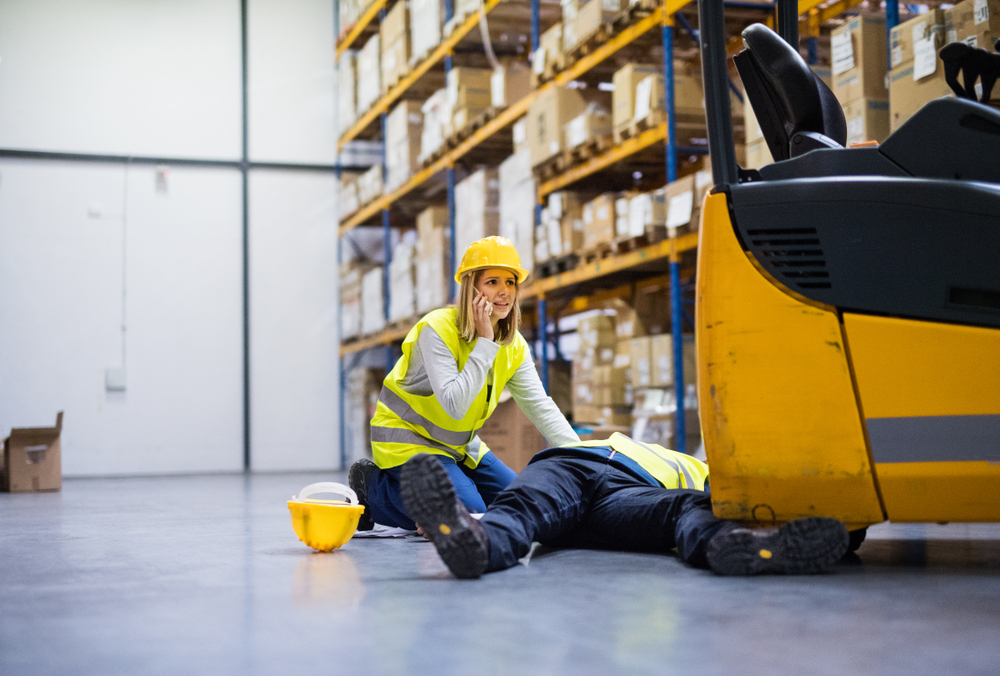
Without a rigorous approach to safety, warehouses can be dangerous places. So, here are the three common warehouse hazards and how to prevent them.
Warehouse hazards come in all forms. Some are completely avoidable by doing something simple, but not necessarily intuitive. Others are things that can’t be prevented and have to be managed or minimized instead. Some of the most common warehouse hazards are a mixture of both.
A thorough risk assessment will go a long way towards identifying and dealing with any potential workplace hazards. If you have a business with more than five people in it, you are legally required to do a risk assessment and record it. If you have less than five people in your business, HSE still recommends a risk assessment — but you don’t need to write anything down.
So, to give you a head start on your risk assessment, here are three common warehouse hazards to look out for and what you can do to stop them.
Warehouse Hazard #1: A Cold Wworkplace
Winter is finally over, but spring isn’t exactly sweltering either. The UK and Ireland have been beset with abnormally cold weather, and it has led many to question how cold a workplace is allowed to be.
For most workplaces, the answer is 16 degree Celsius. However, for workplaces where staff are engaged in physical work, the answer is 13 degrees Celsius. Warehouse work likely qualifies as physical, but maintaining a 13 degree warehouse can be harder than you might think. Warehouses are big, open spaces which aren’t typically insulated very well. When it’s minus 13 degrees outside, you may struggle to get your warehouse’s temperature above freezing.
The cold weather is an example of a hazard that you can’t prevent, but the temperature of your warehouse is something which can modify with decent heating and installation. Beyond that, insist that your staff are wearing appropriate clothing and make sure that they are following your recommendations for staying warm.
Warehouse Hazard #2: Slips, Trips & Falls
Late last year, Poundstretcher was charged £1,000,000 — all because its messy warehouse put people in danger of slips, trips, and falls.
While slips, trips, and falls are perhaps better understood as three separate hazards, they all relate to the same thing: your floor. A slippery surface can often result in a slip, an untidy surface can often result in a trip, and an uneven surface or a heightened surface without protection can often result in a fall.
These types of hazards are common in warehouses because of the sheer amount of floorspace a warehouse tends to have. As such, it’s easier for some corners of your floor to go unnoticed. What’s more, untidy floors are a more common problem in warehouses — where badly stored items can quickly become trip hazards — than in other workplaces.
HSE has a guide on how to prevent slips, trips, and falls which refers to the legislation relevant to these hazards. In a worst case scenario, a slips, trip, or fall can be fatal, but they are not inevitable. They don’t “just happen”, and there is a lot that can be done to make sure that they don’t happen.
As with any other warehouse hazard, a risk assessment will help you identify and deal with potential slips, trips, or falls. However, a floor map is a specific tool HSE recommends you use which will help you to do a risk assessment specifically for your floor.
To prevent slips, simple things like entrance mattings — so that wetness from outside isn’t brought inside — can reduce slips. Spills needs to be cleaned up as soon as possible, but the way in which a floor is cleaned can also drastically affect how much grip it has. Also, bear in mind that some types of floor are inherently more slippery than others, so installing new flooring might be a necessity.
To prevent trips and falls, make sure that guardrails are put anywhere where a fall might happen and that manufacturer’s instructions for mezzanine flooring or elevated surfaces are clearly displayed. Don’t leave things in stairways, throughways, or aisles; storing things properly will help to prevent this.
Warehouse Hazard #3: Misused Racking
Racking misuse can be fatal. Overloading a storage system, ignoring a damaged system, and messily stacking items on top of each other are just some of the examples of racking misuse which can cause severe accidents.
You don’t have to look far to find examples of racking collapses making headline news. When this happens, the best case scenario is that the business loses thousands of pounds due to broken or damaged product and a warehouse in need of repair. The worst case scenario is injury or death.
In order to make sure racking isn’t misused, employers should insist that all employees follow the manufacturer’s recommendations to the letter. Load notices give explicit guidance on how a racking system should be used and what the maximum load for the system should be.
As for damaged racking, employers should be trained on how to inspect a racking system because damage or missing parts are not always obvious. Inspections when a system has been potentially damaged — or even if damage is suspected — is a legal requirement under the Provision and Use of Work Equipment Regulations (PUWER) 1998.
Beyond that, HSE also recommends regular staff inspections and an inspection from a SEMA approved racking inspector once a year. For staff inspections, Storage Equipment Experts recommends and provides racking inspection training for employees and employers. We are happy to deliver this training at your workplace or at our training centre.
To book your racking inspection by SEMA Approved inspector or racking inspection training today, contact us for a FREE consultation.