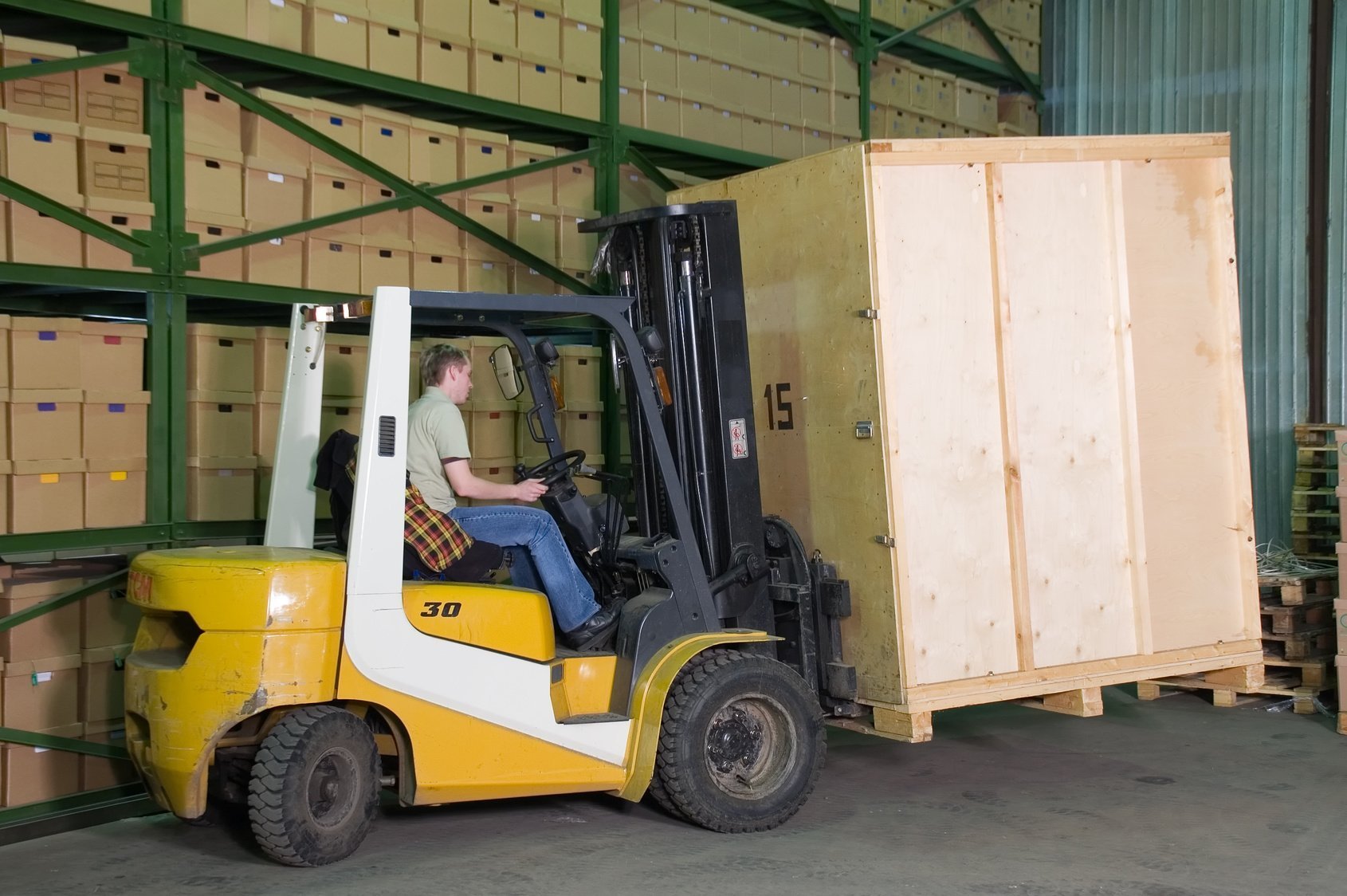
The 14th Annual Forklift Safety Conference takes place at the end of this month and there are plenty of reasons why it affects everyone.
The Forklift Safety Conference has taken place every year since 2002, and it affects a lot more than just forklift experts. With over a million forklifts sold in 2014 alone — that figure having risen steadily for several years — forklifts are serious business.
A warehouse in Telford recently learnt the value of a well-made forklift after its roll cage saved a worker from a potentially fatal racking collapse. All of which brings us to our first top tip for forklift safety…
1. Forklift Safety Should be Partnered with Racking Safety and Warehouse Safety
If pallet racking is properly secured, then it should be able to withstand most forklift impacts. Of course, forklift impacts should be avoided at all costs, and proper use of a forklift will ensure this. However, sometimes, no matter how careful you are, an accident might happen because the environment you are driving in is dangerous and not the forklift itself.
This is why forklift safety should be partnered with racking and warehouse safety. If your pallet racks are loaded properly, then a forklift can drive down aisles without worrying. However, this is permitting that the aisles themselves are free from obstructions or slippery services.
Another way that racking safety should be partnered with forklift safety is with the use of rack protectors. These can — and should — be added to racking wherever there is likely to be a collision. Though this comes with a caveat. Both we at Storage Equipment Experts and SEMA themselves are of the opinion that physical rack protectors are often misused. That is to say, many businesses are often over-reliant on them.
The best form of racking protection comes in the form of prevention and protection. Put another way…
2. Racking Inspections from Racking Inspection Experts and Racking Inspection Training are the Best Form of Rack Protection
They really are. That’s why HSE agrees with us that pallet racking should be inspected by an expert, such as a SEMA approved rack inspector on a regular basis. And regular, in this context, means at least once a year. Added to that, HSE also states that racking requires a more regular inspection from internal warehouse staff. For this, we recommend racking inspection training.
The net result should be racking which is secure enough that, should a forklift bump into it, the system will not completely collapse. Forklift safety should be followed at all times but, should the worst happen, secure racking is there to make sure that a bad situation is not made worse.
3. Warehouse Safety is a Positive Feedback Loop
If you obey HSE’s guidance on racking safety, then you will be safe when something goes wrong with your forklift. If you obey HSE’s guidance on forklift safety, then you will be safe when something goes wrong with your racking. The two disciplines compliment each other well, but this is also true across your whole warehouse.
Your warehouse is a delicate system. When one thing goes wrong, it often leads to other problems. Wet floors lead to slips and trips, which can lead to low employee motivation, unsafe behaviour, and yet more accidents. However, the reverse is also true. That is to say, when things go right it can lead to other things going right.
If you use your forklift properly, then your racking will be safer. And if your racking systems are safer, then your whole warehouse will be safer too. Good things have a way of snowballing in much the same way that bad things do.
Combining forklift safety with racking safety is the best way to ensure that your warehouse is living up to its potential! Contact Storage Equipment Experts, the best racking safety experts in the UK!