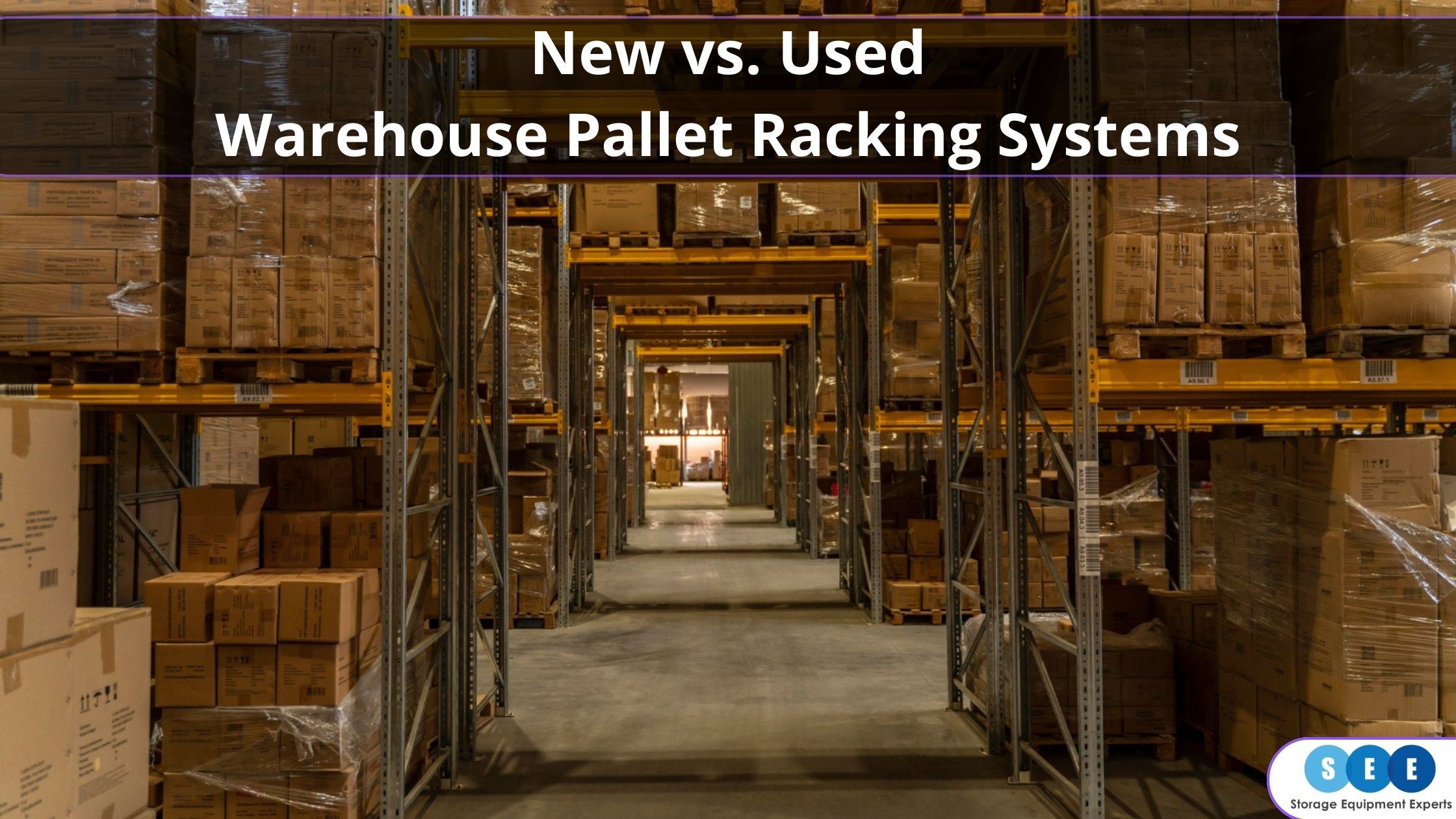
Pallet racking systems are a key part of the set-up and operations of any warehouse – they make storing and accessing your goods as easy as possible and let you make the most of often limited space.
Buying industrial pallet racking systems can require a lengthy review process to get the right system for your space and operations. Among the very first decisions you will want to make, though, is between buying new or repurposing old. The choice between new and used pallet racking systems involves factors like technology, reliability, suitability to specific warehouse requirements, and budget (of course).
In this blog, we’ll look at the advantages and disadvantages of both new and used pallet racking systems, aiming to give you all the tools you need to make the right choice for your warehouse.
Advantages of New Pallet Racking Systems
Latest Technological Features
New pallet racking systems incorporate cutting-edge design and technological advancements. These features enhance performance, efficiency, and durability, presenting a long-term investment.
Warranty and Reliability
New warehouse racking systems will generally come with a manufacturer’s warranty, offering a safety net against defects and ensuring a smoother operation with fewer unexpected maintenance issues.
Customization Options
Most importantly, buying a new racking system means that you have a system built to the dimensions and specification to exactly fit into the available space in your warehouse and to suit the size, weight and access requirements of the pallets or other goods stored within your warehouse operation.
Integration with Advanced Management Systems
These systems can be integrated with modern warehouse management systems, enhancing tracking, inventory management, and overall control – as with the benefits of customisation, the return on investment due to better stock control and management can make the initial outlay more than worth it.
Disadvantages of New Pallet Racking Systems
Higher Initial Cost
The investment in new industrial racking systems can be substantial, impacting the financial planning of businesses, especially smaller ones. The price difference between a brand-new and a used system is usually significant.
Longer Lead Times
Many racking systems are not available ‘off the shelf’ and there can be lead times of many weeks before the racking is delivered, installed and operational – if you need a rapid deployment for a new warehouse or an expansion, then this will need to discussed with your racking supplier to explore the available option.
Depreciation Factor
Like most new purchases, warehouse racking systems lose much of their value over time, which can affect long-term financial planning.
Need for Specialized Training
Implementing new technology might require additional training for staff, adding to the overall cost and effort (as well as the time it takes to see a return on your investment).
Advantages of Used Pallet Racking Systems
Cost-Effectiveness
Used systems are a lot more budget-friendly, making them appealing to businesses looking to save on cost
Immediate Availability
These systems are typically available for immediate delivery to your site and ready for installation without the delays of manufacturing new racking.
Environmental Benefits
Opting for used systems supports recycling and reduces the environmental impact associated with new production – which may appeal to companies that want to establish their credentials as being green in business.
Disadvantages of Used Pallet Racking Systems
Unknown History and Wear
The previous use of these systems can raise concerns about their structural integrity and safety – you can’t know how well they have been maintained or if the previous owner has covered up any issues to inflate the value, for example. Second hand racking systems have often been stored outside and exposed to the weather which is often confirmed by corrosion to the components
Limited Customization
Used racking systems offer minimal (or, often, no) customization, often leading to space utilization inefficiencies or challenges in accommodating specific storage needs. Making the most out of every square foot of floor and air space is of the utmost importance in warehouse management – so this can be a deciding factor. Worse than this, it is common that racking bought as second hand equipment is the incorrect size for the pallets stored onto the racking. Second hand goods which includes racking is often bought as seen and its up to the person purchasing the items to ensure that it is suitable for the intended use. A second hand dealer can only offer the systems they have available which might not be the correct size or type to optimise your storage needs. Pallets stored incorrectly onto racking that is the wrong size can increase the risk of a pallet failure and this can lead to a racking failure.A supplier of new racking can offer a choice of different racking systems in an almost unlimited set of dimensions to exactly suit each set of warehouse operation requirements.
Absence of Warranty
Without manufacturer warranties, any system failures or maintenance fall on the business, potentially negating initial cost savings (if there is an issue).
Making the Right Choice for Your Warehouse
Unfortunately, buying used pallet racking comes with hidden risks as the history, strength, suitability and condition of the racking is largely unknown and its common that used racking systems are not suited to the exact requirements of a warehouse operation which can reduce the efficiency& safety of your warehouse operation.
Whether you choose new or used, you will need to ensure your racking is assessed by SEMA-approved racking inspectors. Get in touch with the team at SEE Racking Inspections today to book your consultation.