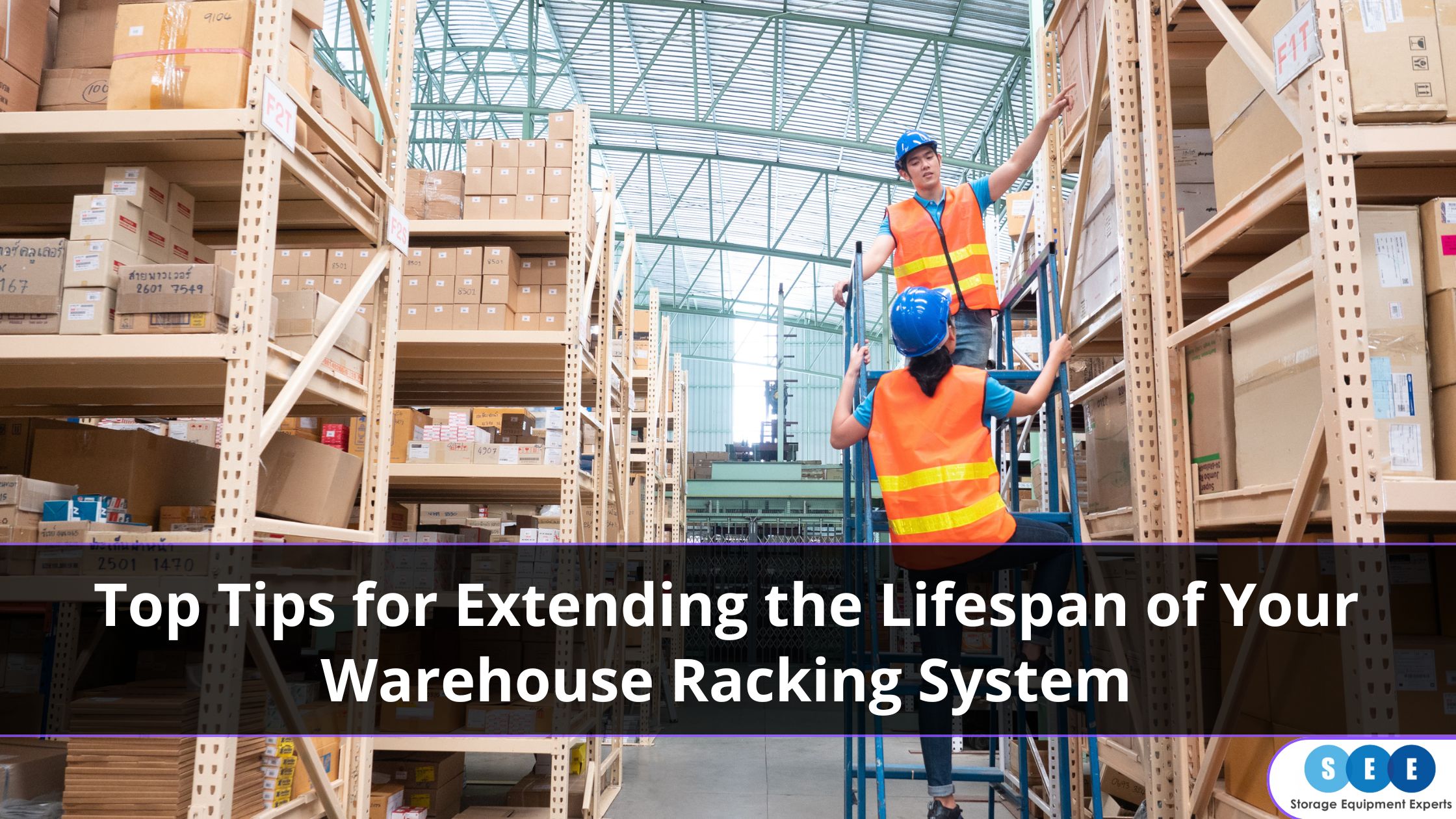
Warehouse racking systems are the backbone of efficient storage operations. However, like any equipment, they require proper care and maintenance to remain safe and functional for as long as possible. You can significantly extend the lifespan of your racking systems by taking proactive measures and following best practices, saving your business money and avoiding costly repairs or replacements.
This article will guide you through essential tips and strategies for preserving the integrity of your warehouse racking.
1. Conduct Regular Inspections
Routine racking inspections are the first line of defence against wear and tear on your racking systems. Regularly checking the racks means you can catch minor issues before they escalate into major problems that compromise the safety and stability of the entire system.
What to look for:
- Bent or Damaged Racking Components – check for any signs of bending, dents, or other deformations. Even a slight bend can indicate structural weakness and may lead to collapse under heavy loads.
- Loose or missing beam safety locks – ensure that all beam safety locks are present and installed correctly. Beam safety locks are an essential safety component that help to maintain the location of the beams into the vertical uprights.
- Check that pallets are the correct type and size, free from damage and stored correctly onto the racking systems.
- Load safety notices are clearly displayed on the ends of the racking systems.
- Floor fixings are installed correctly and free from damage.
- Corrosion and Rust – look for signs of rust or corrosion, especially if your racking system is made of metal. Rust weakens the structural integrity of the racks over time.
Tip: Create a detailed rack safety inspection checklist and have a designated team member or safety officer conduct these inspections regularly. Keeping a record of all inspections helps track any recurring issues.
2. Train Employees on Proper Handling
One of the most common causes of racking damage is improper handling by warehouse staff. Proper training on how to use the racking system can prevent a significant amount of unnecessary wear and tear.
Key areas of training:
- Safe Loading: Teach employees the importance of following weight limits and distributing loads evenly across the racks. Overloading or uneven weight distribution can cause beams to bend and weaken.
- Correct use of Forklifts: Forklift collisions are a major source of racking damage. Train operators to handle forklifts carefully, especially when manoeuvring near the racking systems. Emphasise the importance of avoiding direct contact with the racks.
- Reporting Damages: Encourage staff to report any signs of damage immediately. Early reporting allows for prompt repairs, preventing minor issues from becoming severe problems.
Remember: Investing in regular training sessions can go a long way in preserving the lifespan of your racking systems. When employees understand the impact of their actions, they are more likely to handle the equipment with care.
3. Perform Routine Maintenance
While inspections help identify problems, routine maintenance is the grease that keeps your racking engine running smoothly. Regular maintenance should mean that minor issues are addressed before they lead to costly repairs or replacements.
Maintenance Checklist:
- Tighten Bolts and Fasteners – check all bolts and fasteners regularly and tighten any loose ones. Even slight loosening can compromise the stability of the entire structure.
- Replace Damaged Components – if you notice any bent beams, cracked supports, or other damaged parts, replace them immediately. Using damaged components increases the risk of racking failure.
Pro Tip: Schedule maintenance activities during off-peak hours to minimise disruption to your operations.
4. Use Protective Barriers and Guards
Installing protective barriers and guards can prevent accidental damage to your racking systems. These safeguards act as a buffer between the racks and moving equipment, reducing the likelihood of collisions.
Types of protective equipment:
- Rack Guards: Installed at the base of the racking system, these guards protect the lower parts of the racks from forklift impacts.
- End-of-aisle Barriers: These barriers are placed at the end of the aisles to prevent equipment from hitting the corners of the racking system.
- Column Protectors: Attached directly to the uprights, column protectors shield the racking columns from potential impacts.
Recommendation: Consider installing these protective devices, especially in high-traffic areas where the risk of collisions is greater.
5. Monitor Load Distribution
Proper load distribution is key to maintaining the structural integrity of your racking system. Uneven loads can cause the racks to become unbalanced, increasing the risk of tipping or collapse.
Best practices for load distribution:
- Follow Weight Limits: Each racking system has a specified weight capacity. Make sure employees are aware of these limits and adhere to them strictly.
- Distribute Weight Evenly: Place heavier items on the lower shelves and lighter items higher up. This helps maintain the stability of the racking system and reduces the risk of tipping.
- Use pallets correctly: Ensure that the correct type and size pallets are placed squarely onto the racking to ensure a UDL (Uniformly Distributed Load). Improperly placed pallets can create uneven pressure points.
Note: Implement a policy for regular checks of load distribution, especially after large deliveries or when reorganising inventory.
6. Implement a Rack Safety Program
A comprehensive racking safety program means all employees know the best practices for handling and maintaining racking systems. This program should include training, regular safety meetings and clear guidelines for reporting issues.
Key elements of a safety program:
- Regular Training Sessions – offer periodic training to refresh employees’ knowledge on racking safety and handling procedures.
- Safety Inspections – schedule regular safety inspections conducted by a qualified inspector to identify and address potential hazards.
- Clear Reporting Procedures – Establish a system for employees to report any damage or safety concerns immediately.
Benefit: A proactive safety program both extends the lifespan of your racking system and creates a safer working environment for everyone.
Conclusion
Extending the lifespan of your warehouse racking system requires a combination of regular inspections, proper maintenance, employee training, and the use of protective measures. These proactive steps will let you keep your racking systems in excellent condition, reduce the risk of costly repairs and (most importantly) maintain a safer warehouse environment.
Investing time and effort into maintaining your racking system pays off in the long run, leading to smoother operations and greater overall efficiency. You can find out more by visiting the SEE Racking Inspections website.