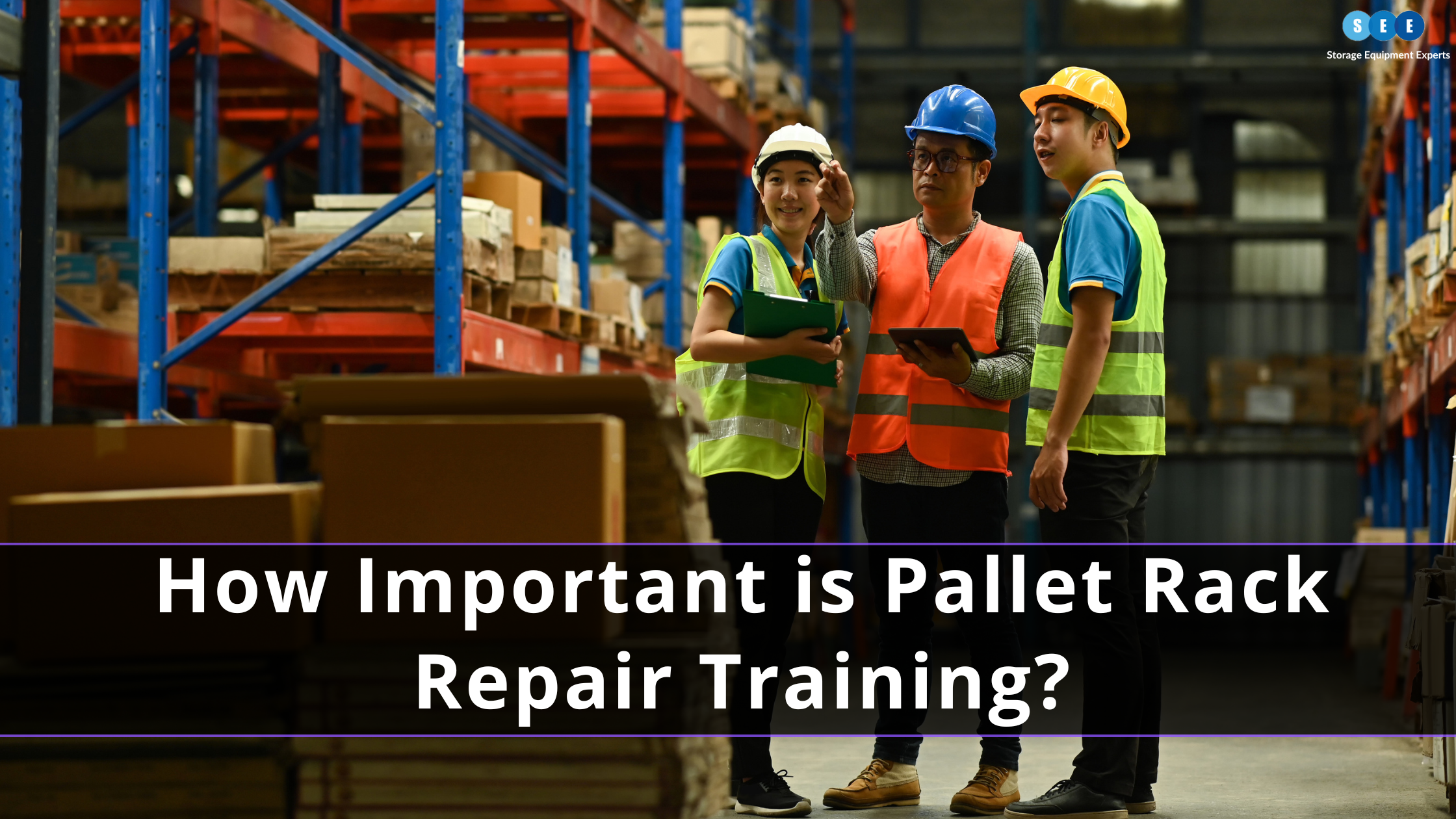
Enhancing Warehouse Safety and Efficiency
Pallet racking systems are indispensable to warehouse operations, providing essential support for storing goods efficiently and safely. However, as valuable as they are to operations, they can be just as dangerous if they are not rigorously and properly maintained.
A large part of maintenance is identifying an issue – the earlier a potential problem is noticed, the better. Thereafter, the role of maintenance shifts to repair. In this article, we’ll take a look at how pallet racking systems can suffer damage over time, posing significant risks if not properly maintained.
Understanding Pallet Rack Repair
As noted, pallet rack repair involves dual aspects. First, there is the identification of the potential issue, then there is the repair. When conducting a pallet racking inspection, it is good practice to focus on the most common issues, including:
- Bent beams – these are often caused by forklift or other manual handling equipment impacts.
- Loose bolts – this can occur due to frequent vibrations from loading/unloading and traffic passing by.
- Rust – humid or wet environments and untreated metals will result in rust.
- Displaced unions/joints – as with loose bolts and bent beams, joints and unions can be forced out of place through heavy use.
- Cracks – robust as they are, pallet racking systems can be subject to slight defects in the manufacturing process, fluctuations in temperature, and other factors that can result in cracks of all sizes.
Any one of these issues can compromise the overall integrity of the structure, as well as dramatically reduce the lifespan.
Never forget that repairing these damages is not about maintaining aesthetics; it’s about ensuring the safety and functionality of the warehouse and all personnel within it. Ignoring these issues can lead to severe consequences, such as rack collapses, injuries, and significant downtime.
Benefits of Pallet Rack Repair Training
Investing in pallet rack repair training offers numerous benefits, directly impacting safety and efficiency within the warehouse.
Key Benefits
- Improved Safety – Proper training helps prevent accidents by ensuring that racks are repaired correctly and promptly.
- Operational Efficiency – Well-maintained racking systems minimise downtime, keeping the warehouse running smoothly.
- Cost Savings – Effective repairs reduce the need for costly replacements and extend the lifespan of racking systems.
Warehouse managers who equip employees with the necessary skills to inspect and maintain pallet racking can maintain a safer environment and avoid the high costs associated with neglected repairs.
Key Components of Effective Repair Training Programs
A comprehensive pallet rack repair training program should cover both theoretical knowledge and practical skills. This balanced approach ensures that employees are well-prepared to handle a variety of repair tasks.
Training Program Components
- Theoretical Knowledge: Understanding racking structures, load limits, and common types of damage.
- Practical Skills: Hands-on repair techniques, including straightening beams and securing bolts.
- Safety Protocols: Emphasising the importance of following safety guidelines and compliance with industry standards.
Incorporating these elements into the training program ensures that employees are equipped with the skills and knowledge needed to perform repairs safely and effectively.
Implementing Repair Training in the Workplace
Integrating repair training into regular warehouse operations requires careful planning and execution. Here are some steps to ensure successful implementation:
Implementation Steps
- Regular Training Sessions: Schedule periodic training and refresher courses to keep skills sharp.
- Experienced Trainers: Use knowledgeable trainers who can provide real-life scenarios and hands-on guidance.
- Practical Scenarios: Include exercises that mimic actual repair situations to give trainees realistic practice.
Managers can ensure that employees are always prepared to address any issues that arise by making repair training a regular part of warehouse operations.
Enhancing Safety Through Repair Training
Proper repair training directly contributes to a safer warehouse environment. When employees are trained to identify and fix issues promptly, the risk of rack collapses and related injuries is significantly reduced.
Safety Enhancements
- Risk Reduction: Regular inspections and immediate subsequent repairs prevent minor issues from becoming major hazards.
- Injury Prevention: Well-maintained racks reduce the likelihood of accidents, protecting employees from harm.
Emphasising repair training ensures that safety protocols are always followed, creating a more secure workplace.
Boosting Efficiency with Well-Trained Staff
Efficient repairs by trained staff can significantly boost overall productivity in the warehouse. When employees can quickly identify and address issues, operational disruptions are minimised, meaning that normal business can continue without pause.
Efficiency Boosters
- Quick Issue Resolution: Trained staff can handle repairs swiftly, reducing downtime.
- Extended Racking Lifespan: Proper maintenance extends the useful life of racking systems, leading to long-term cost savings.
- Improved Workflow: Efficient repairs ensure that the warehouse operates smoothly, enhancing overall productivity.
Well-trained employees contribute to a more efficient and effective warehouse, benefiting the entire operation.
Conclusion
Pallet rack repair training is an absolute must for warehouse operators looking to maintain a safe and efficient site. Giving staff the autonomy and skills to understand the pallet racking systems they work with on a day-to-day basis means that accidents will be reduced – as will operational downtime and unnecessary costs.
Investing in comprehensive training programs is a proactive step toward ensuring a secure and productive work environment. For expert guidance and comprehensive training solutions, visit SEE Racking Inspections.